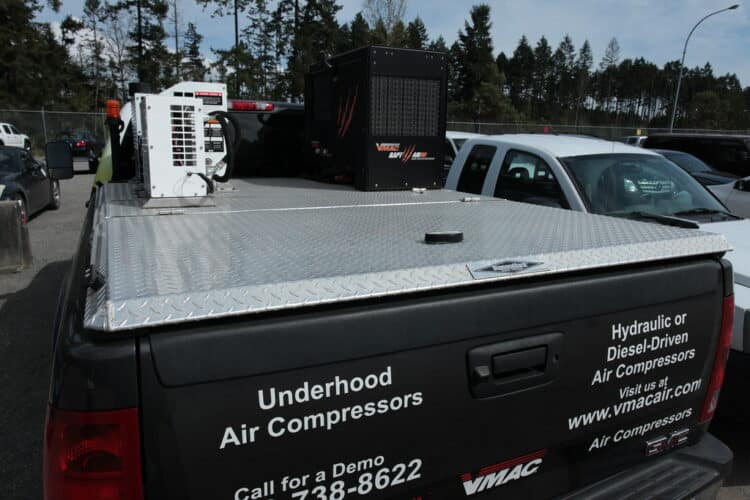
Are you wondering how much does it cost to replace a compressor or how long do air compressors last? Maybe you’ve asked: can air compressors be repaired?
These questions may have been bugging you since you have purchased a new one for personal use. You want to get the best out of it, but you are worried that you might not be using it correctly or straining it too much. You want to put all your worries to rest and at the same time use it for your hobbies without making mistakes.
Here is some useful information that you should learn to relieve you from all your compressor-related concerns.
Table of Contents
A Preview
Pressurized air instruments serve as the anchor for all manufacturing companies, are beneficial in medical practices, and are primary devices for the proliferation of the foodservice industry. People do not know how these unsung and often underappreciated devices are used to make things run better, smoother, and faster. These wonderful tools have not always been deemed as essential pieces of machinery compared to others and are often relegated to the background. Your perspective will change after reading this.
Compressed air supply systems allow for more than adequate power for many industrial applications. This type of power output is crucial for production and manufacturing, which will provide the needed employment to people and also teach them new skills.
Operating these complicated devices is not easy. You should be very careful and aware of how each part of the machine works in the bigger picture. You should know proper safety procedures in case something malfunctions and possible cause bodily harm.
Even when a lot of companies in many industries rely on these powerful instruments to supply power to keeps things running, they would rather spend money to fix them than replacing them. Even when compressor repairs cost more than buying a new one, they would still prefer the former.
So you have two choices once something in the air compressor malfunctions: either buy a new one or get it fixed. So read on, and once this happens to you, you will know what is the most appropriate option to choose for your device.
What to Do if You Own One
So the question: “Can compressors be repaired?” is a loaded question and cannot be answered instantly. You have to know at which point in the impairment of the device should you get it fixed compared to buying a new one and which way would cost lesser in the long run.
Lucky for you, experts have studied this particular brain-teaser and provide an underlying structure on what are the best steps to take that would be the most advantageous for your business.
According to them, if you think about the total price of the new compressor system, presuming that it would last for more than ten years, the acquisition would only account for 12 percent of the overall cost it incurs. Besides, 76 percent of the total pricing of owning one would come from electricity bills.
To regard this monetarily, if you steadily run a powerful factory-owned compressor for ten years, you will spend less than 80k dollars in electricity cost.
If you are judging the purchase of the device by the cost alone, then you have to be aware of the additional financial burden will incur to you as time passes. Even if at first it would appear that getting it fixed would cost less than replacing it, which in truth is the opposite. Think about all the hassle in repairing and the incurring cost. Is it worth it?
The compressor repair cost will manifest in different ways. As time passes and the device gets worn out by use, the cost of fixing it will get higher. Some parts will need cleaning, repairing, or replacing. That is why you need to seriously mull over the price of air compressor repair that will be 50 percent more compared to replacing it. Also, think about the ensuing pricing for rebuilding an old air compressor because malfunctions would always be apparent due to its age. Old model types are known to be inefficient in the long run, so you might end up spending more on making it always running rather than spending on a new one.
How to Trouble-Shoot the New Compressor
Even though it may seem to be more advantageous to replace it rather than fixing it, whenever it malfunctions, it would be favorable to you in knowing simple trouble-shooting. You do not need to spend on either option if you can have it fixed in-house. Additionally, by being fully informed by the intricacies and possible difficulties within the device, you can make a better judgment of which choice might cost more or less.
Here are some of the usual problems that might be the root causes of affecting the device:
• Many defects that may result in an air compressor repair come from the electrical power source. There might be connection issues between the device and the power lines.
• The device’s lubricating quantity might be too low and can contribute to inadequate functioning. You have to make sure the amount of oil in the system is more than adequate.
• If you hear something is knocking around within the machine while in operation, a loose component like ball bearings, belts, or other defective parts is the likely reason. If you can find out and remove the errant part, you can make the necessary alteration or direct the repairman where exactly it is, so you would not have to spend more than you should.
• Oil-related problems can cause the device to not function properly, as too much intake of oil, milky white discharge, loose parts in the oiling system, and many more.
• Other common issues that usually happen are concerning piston rings that get worn-out due to use and problems with air ventilation.
• These system flaws can be fixed by a few adjustments and replenishing new components from old ones. More severe problems may need larger replacement parents or may call for a total overhaul of the system.
• You have to know that malfunctions happen across the overall system itself and not only within the device. An example is an end-use pressurized air that may be lacking or may leak out from the piping. By further inspection, you will find the leaks and do something to fix it. If you will discover that the reason for the end-use defecting pressure due to corrosion in the piping of insufficient quality of air, you may need to make an investment by replacing the whole system of air pipes and only use clean air for intake.
• If it is always exhausting hot air, then the issue is in the mechanism for cooling. You can either fix or replace it, which will depend on the strength of the mechanism.
• The compressor belting will wear down after some time. The causes will either be the tightness or looseness of the alignment. If you have the capability of adjusting them yourself, then do so, but you also have to know those belt misalignments are caused by someone who did not adjust them properly. If your or your in-house maintenance people could not make the correct adjustments, then hire an outside professional, and you can save cash that way in the long run.
• The device’s electrical fuses should be the correct size, or else you will notice that replacement happens a lot because it tends to blow up repeatedly. So make sure to get the appropriate fuse size so you can save cash for the long haul.
• Blown fuses do not have the same solution as the issue of repeated resetting of the device’s reset mechanism. It is not because of something of the wrong size, but a serious defect in the motor which immediately needs professional technical assistance.
The cost of air compressor repair will likely be compared to hiring an outside technician. So be sure you have some basic trouble-shooting knowledge so that you can properly diagnose what the device needs. It will enable you to save as much cash as possible as time passes.
Get a Professional Technician if Trouble-shooting Would Not Work
You need to know that you have done everything within your trouble-shooting power to avoid expensive repairs. You should also be aware of the right time to bring in a technician that is specifically suited for air compressor controller repairs.
Getting professional consultation can be thought of as a learning experience made up to teach you the best way to fix a particular malfunction and spending the least amount of money. A pro technical helper can shine a light on the most cost-cutting measure you can take either by replacement or fixing.
Yet this is the most practical way in finding a solution to get it repaired if you are still unaware of the malfunction. The pro can give a thorough analysis of the situation and provide the best advice. They can tell you if the device is performing in its best capacity or not, or how many years it can go on running, or which parts need replacement.
A lot of compressor operators want this type of professional examination for the device if it has been running for quite a while and maybe past its shelf life. Even though the device might be functioning great, it may be passed a stage of longevity that fixing it might not be cost-effective anymore. Furthermore, when a company that relies on pressurized air systems does not have a new compressor to use, there will be employee downtime that would result in losing the company money. By looking at the rising cost it incurs, fixing it would need to be a priority.
Nevertheless, a thorough analysis by a professional technician will help you understand and find the best solution for compressor repair.
‘Can Air Compressors Be Repaired?’ and other Queries Relating to Replacement Parts
There is a middle point between a small compressor repair patch up and replacing the whole of it that companies need to think about.
Companies are hardly observant in looking over the different ways End-Use tools are imposing on energy-saving matters. Putting too much-pressurized air on end-use devices is a method that wastes power as time goes by. Small and mid-level adjustments can save you time and finances and also lessening the strain on the device.
If End-Use instruments get wearied by constant use, exchanging each errant part can save energy. Old model End-Use devices are not made to save power so you need to think about substituting them be better and top-class models.
You should also need to be aware of the particular tools and equipment that need to have the most pressure. If you have found out they require less pressure, then you can reduce the total air system pressure or replace it with a better model.
Other available parts can be set-up that can save you financially that aren’t End-Use tools. However, they are money-savers in the long run by lowering the consumption of energy. A good example is the installation of top of the line piping, which can decrease the risk of mistakes in rendering pressurized air to end-use devices. Effectively branded air dryers can minimize the wear and tear in pipes and can better the end-use tool’s viable functioning by moisture reduction. They can also help in cutting down costs by being more efficient.
Finally, if you purchase the best air filters available for the device, then it can do its function efficiently and will save you finances for repair or replacement as time passes.
The bottom line is: you need replacement parts available at all times, in case something malfunctions and needs compressor motor repair. By investing in particularly essential compressor components, you can prolong the shelf life of the device so that it can still be of good use for the time to come.
A Long-term goal in Saving Money for the New Compressor
People are looking for ways to lessen air compressor repair costs as the advent of technology arrives in the form of newer and better models. It is significant to note that they are particularly designed to be less expensive to purchase and would incur lesser costing in repairing.
There are a few ways how these newer model-types can be cost-saving over time:
• Proper sizes: In times, when electricity costs go down, factories set up new compressor replacements that are comparatively larger than the usual. They did this because they weren’t thinking of rising energy prices but how it could do more work for the factory if it might become more successful in the future.
However, a larger one consumes a lot more electricity and will incur higher maintenance costing in the current time instead of saving money in the future.
In any case, some companies did not plan thoroughly and did not have enough knowledge about the overall costing of operation and maintenance. They may have purchased too much of the device that they could financially handle.
Some companies did not even think that the device can play a crucial role in the growth of their respective companies, and as a direct result, the device did the opposite as intended and blocked the development of the company. Thus, haltering profits in the future.
To make things better for compressor-dependent companies, purchasing properly-sized ones will incur more profits and lower the finances for operation, which in turn, enhances employee productivity.
At this point in the companies’ realization that they want internal improvement, they need to bring in a professional to analyze the device to further enhance it and find energy-saving measures. The pro will then suggest which parts often need replacement and tell you the many benefits of a properly-sized device.
• Using the energy-saving design to its full capacity: As electricity prices rise constantly, the makers have found ways to make the compressor operational energy costing become lower. As time goes by, investing in the newest, top-of-the-line energy-saving models can be economical and can save 30 to 60 percent in electricity billing prices over the entire lifespan of the device.
Designers have discovered ways to make the device more effective by making them run in varying degrees of acceleration, and some run in modulated speed. It is an effective method in getting End-Use devices the right pressure, yet it is an ineffective way to cut energy usage. Even though the device is turning in 20 percent of the pressurized air to end-use tools, it is still taking up to 70 percent of its total energy capacity.
Fortunately, the makers have found a solution for this issue by creating a better and more effective compressor mode functionality. The first button is for loading/unloading, which utilizes air stored in the tank to preserve pressurized air while the primary one overuses air pressure. The amount of unloading time will cut down energy use within the range of 10 to 25 percent during the whole loading time. Yet, these schemes are only as effective as the availability of storage in the system. The more time the entire system can function in the unloading button, the lesser the electrical energy is utilized. If the device has to come back to the loading function too rapidly to respond to the requirement of End-Use tools, power savings costs will be lessened.
There is a new model compressor that has a better connection between energy usage and requirements for end-use air compression, called the “Variable Speed Control” compressor. This type of device can only produce and turn in the precise quantity of pressurized air that is needed in the whole system at any particular time. It is advantageous for operational tasks that do not need excessive pressure most of the time. The disadvantage is they do not function efficiently compared to the traditional models when operated in a fully operational capability. So it is not ideal for systems that function at maximum capacity for the whole day.
Another newer design is called the “Variable Displacement Control” compressor, whose chief function is to make proper adjustments of the device’s overall capability in conjunction with end-use necessities. When you take off 50 percent of the device’s total workload for the whole day, this control mechanism will lessen the size of the device for the time. Yet like with Variable Speed Control models, they become ineffective at the maximum workload. So it should only be used sparingly in different functions that have varying requirements for end-use tools.
Rebuilding an old air compressor can sometimes work better if you do not want to get newer and better models. You only have to add either the Variable Speed Control of the Variable Displacement Control in the system. However, these particular attachments are expensive to undertake and should only be utilized for large factory-used compressors that are too costly for total replacement. If your business is small, getting a new one is generally a better way to save your finances.
About Quincy Air Compressor Repair
If you are still hesitant on what is the best way to deal with either total compressor replacement, compressor repair, or merely substituting errant parts, Quincy Compressor will help you decide and make the most of its capability.
If what you are looking for is fixing your device, some Quincy-related professional technicians can make a total overhaul of your air supply system. They have ways to take your often malfunctioning system to topmost running capability. They also have top-of-the-line new compressors that are unmatched due to their strength and power. Possible malfunctions can be dealt with by habitual maintenance, replacement part, and periodic repair.
If you want to know the best options for your device, Quincy is there to give you everything you need like sound advice and expert analysis. They can also help you make correct decisions for the betterment of your company. They have developed a comprehensive examination that you can apply for your device called “Energy Quotient,” which has aided many companies. It has helped them find their defects and taught them which tools to use to lower energy costs and increase efficiency.
Quincy is the industry leader that provides the best quality and most energy-saving new compressors in the market today. No matter what kind of compressor-related new business you have, Quincy has the right device for you that is perfect for its growth and development. So if you want to replace your old-model device with a fantastic new one that will work well for a long time, Quincy is there for you. They have the most durable machinery, has energy-saving mechanisms specifically designed within, and a highly-efficient and futuristic design.
Can You Fix Air Compressors?
Is your new compressor on the fritz and stopped running entirely? Well, you can save loads of cash by repairing it yourself. You may have a defective unloader valve that can make the engine cease operation. It is an easy fix because you can buy extra valves at your nearest hardware stores, which are cheap. Once you have one, you would not have a hard time replacing it.
Substituting the Valve
When you first turn it on and worked fine for a few minutes, then stalls and let out loud buzzing noises after many tries, your valve is defective. Compressor air end repair will be uncomplicated if the problem is only a malfunctioning unloader valve. You will know when it is working the right way when it makes a “pffsst” sound after the engine turns off after getting the correct pressure needed. What is happening is that the device is ventilating the extra pressure from the device so that it does not have to exert itself too much when it restarts again.
The valve is constructed within the assembly on the pressure switch, so if you need substituting one, you can call the manufacturer of the device and get a new assembly piece. You will spend about $20 for a replacement.
Before replacing it, be sure the compressor is unplugged. Then, depressurize it by opening the valve below the air tank.
With both hands, fasten two wrenches on the compression attachment and unscrew the nut-free on the airline. Then take it out.
Unplug the cables from the pressure switch and take out the old switch. Then link up the new switch, which already has the unloader valve as part of it.
The Tools that You Need for this Fix
You will need the right tools to complete the easy repair. Here is what you need: slip joint pliers, a 4-in-1 screwdriver, a wrench set, and an adjustable wrench.
A Summary
Now you have learned everything about compressor repair, maintenance, troubleshooting tips, and a lot more. Also about Quincy compressor repair, the most trusted name in the compressor replacement and installation in the whole industry. Whenever something in the device malfunctions, you would not be worried or afraid anymore because you are confident that you know what to do. The air compressor, with all its complications and intricacies, can be managed with the right know-how and abilities.