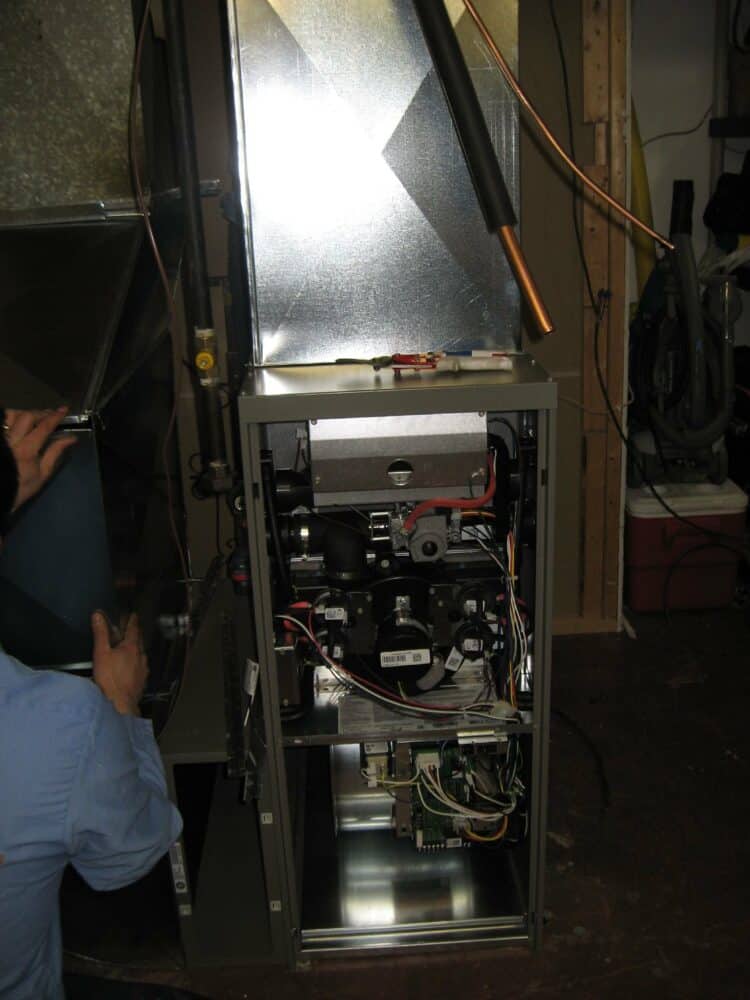
Forced air heating is the preferred method of heating, replacing traditional steam and hot water systems.
Almost all forced-air heating systems use the furnace. You can find gas furnaces in various sizes, types, and even efficiencies according to its application.
How do you pick the right one?
Table of Contents
Basic designs of furnaces
Depending on the fuel source, a furnace consists of two to three main parts.
Gas furnaces, ones using propane and oil, use burners to burn the combination of fuel and air. It then transfers heat to the air through heat exchangers. Electric furnaces use heat exchangers to convert the electricity to heat. And it uses a blower to distribute the warm air throughout your home.
Furnace burners
There are three burner options, and each operates in its unique way.
Single-stage burners
These are the most common burners. With a single-stage, the operation modes are either on or off. And regardless of the conditions, the furnace will operate at the rated capacity. That makes it inefficient, especially when conditions are mild.
Two-stage burners
These burners have three operation modes. That is high fire, low fire, and off, which addresses the inefficiencies that single-stage burners have.
At the high fire operation mode, the furnace produces its full rated capacity, as is the case with a single stage.
Low fire operates at the factory set rate, which is usually lesser (40 to 60 percent less) than at the high fire mode. That way, the furnace meets the heating requirements of the home in mild conditions. The result is lower fuel bills because of improved efficiencies and more comfort.
Modulating burners
These burners offer the most efficiency. And can operate at almost any output within its least and maximum range.
It reduces temperature swings that you are likely to experience with the first two options. That is by continuously checking conditions inside and outside the house.
Modulating burners then adjusts the output to match the conditions. That leads to maximum efficiency and even lower fuel bills while still satisfying your heating needs.
Comparison
If you compare the average temperature and fuel usage of all three furnaces, you can see the temperature differences. In comparison, the modulating and two-stage furnaces maintain a more stable warmth than the single-stage furnaces.
The two-stage furnace offers an 8 percent savings. While the modulating furnace provides a 10% savings as compared to the single-stage furnace, assuming that all of them have an equal rated efficiency.
Furnace blower options
There are two primary varieties when it comes to blowers, the multi-speed and variable-speed blowers. An installer selects the speed for the various types of operations during the installation of the multi-speed blower.
For instance, the installer may select low heating speed, medium cooling speed, and high fan operation speed.
However, the blower will not respond to changes in the operations, such as a clogged filter. And instead, it operates at the selected speed when the furnace requires that operation.
An installer also sets the operating conditions of the variable-speed blower. Even so, the installer does not select the speed for the air rate flow.
Instead, the speed corresponds to a particular air flow rate. The furnace adjusts the blower’s action to fit in with the temperature and information garnered from the furnace monitoring.
That way, the variable speed blower provides the ideal comfort by responding to the changes in conditions outside and inside the home. But that is not all.
Furnaces control the blower through ECMs. These are electronically commutated motors mainly used in variable-speed blowers.
ECMs have flexible program design options that allow them to respond to the circumstances of the system quickly.
Plus, they reduce the electrical costs of running a furnace by at least 25 percent. At the same time, they provide the utmost comfort.
If you are looking for a cheaper option, then constant torque motors are it. They use the technology the ECMs uses but minus the programming. The constant torque motors are almost as efficient but do not respond to changes as quickly as the
ECMs nor as often.
The Annual Fuel Utilization Efficiency Rate (AFUE)
AFUE is a measure of the efficiency of a furnace. And it ranges from the federally required minimum of 80 percent up to 97 percent.
The most budget-friendly furnace models usually have an 80 percent AFUE, multi-speed blowers, and single-stage burners. And that is what most manufacturers bring to the table. But it’s not uncommon to get models rated 90 percent AFUE or even higher.
In most cold climates, an AFUE rating of 90 percent is the federal requirement. Models with that rating or higher often use condensing technology for taking the most heat possible from combustion. Water vapor released from combustion usually condenses into liquid in the condensing furnace.
Although this rating is an incredible way for you to compare the energy efficiency between models, it may inaccurately reflect the unit’s competence as soon as you install it. Other components and processes can affect the operational efficiency of your furnace. It includes humidifiers, filters, duct sealing, routing, and insulation.
For optimal comfort, you must address any prevailing problems with these components so that your system can achieve utmost efficiency.
Furnace’s orientation options
There are several orientations that furnaces can use according to the type of installation. These include low boy, upflow, horizontal, and downflow.
Even so, you can install a furnace in different orientations instead of choosing just one. These are multi-position orientations, or you can combine possible options such as horizontal and upflow.
Upflow
Upflow furnaces are often typical when the ductwork is overhead the level of setting up the unit. That can be because you have the heating system in the basement or closet.
In upflow orientation, the air moves in the furnace from below and gets out after heating at the top. The return air connection is often at the bottom of the heating system.
Or at whichever side of the blower compartment.
Downflow
With these types of furnaces, the ductwork is below the furnaces. This type of application is common in commercial buildings where the ductwork is inside the slab or underpasses.
The return connection is at the upper part of the furnace and supplies heated air out the lower area. The return air transmits straight to the upper part of the furnaces.
Horizontal
The supply and return connection are at either side of the unit and connects horizontally.
This type of orientation is common in areas with restricted height, such as attics and underpasses.
Low-boy furnaces
These types of orientation result in installing at the top of the furnace both the return and supply connections. That way, you end up with a shorter and broader unit.
Low boy furnaces are out of date, and other types of units are slowly replacing them. Although you still require a duct reconfiguration, replacing a low-boy furnace with an upflow furnace is more suitable.
Venting configurations
There are two main venting structures in furnaces. The first is chimney venting, characterized by sizeable vent connections and found in at least 80 percent of AFUE furnaces. This configuration relies on the ability of hot air to float to dissipate combustion gases and pull fresh air into the fresh air. However, the process works best in large chimneys.
The second is direct venting, which allows exhausting both vertical (by a ceiling) and horizontal (by a side wall). This configuration is typical in higher efficiency furnaces because of the built-in inducer blowers that help with the exhaust spent gasses and drawing in the fresh air. It draws air directly from outside, and a smaller chimney will suffice.
Final take
When picking a furnace, you can consider all the options highlighted, from the venting configurations to the type of blower, orientation, AFUE rating, and burners.
That way, you can pick one that suits your needs and satisfy your heating requirements.