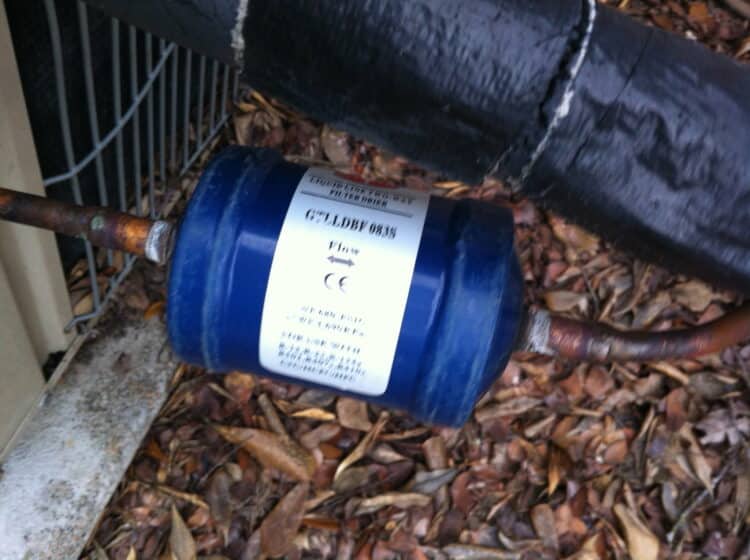
Lots of people all over the world use air compressors in their daily lives. Yet if some brought it in from of you and asked to explain how it works, could you do that? I think not.
You may have seen some guy use it in the past and maybe a little familiar with how it functions. But knowing the ins and outs and the mechanics of its intricate machinery is something you do not get by a glance.
There are many applications for this highly efficient machine. To get to that point, you need to go back to the basics, on how it came to be.
Table of Contents
Some Background History
In going back to the Stone Age, the time when early cave-men discovered the usage of fire. They may not know about the crucial sciences, like physics and math, they had known about constricting the air in their lungs. By withholding air a bit then blowing on the flames, they may have found out that it will develop into a better and more sensational source of energy.
A good expanse of centuries later, when men became a little bit smarter and discovered the usage of tools in the Ages of Bronze and Iron, they began to experiment with compacting air.
In China, during the time where major discoveries were made in the Han Dynasty, bellows were invented that were powered either by foot or by hand. They employed this to stir up the flames in furnaces to create magnificent tools and weapons. It was done in the 3rd century BC.
Eons later, in the year 1762, an engineer by the name of John Smeaton formulated a way to contract air in massive amounts. In this, a water wheel was created to magnify power towards a moving cylinder or a piston that compacted air in an enclosed chamber.
His major discovery contributed to other creations. A few years later, in 1776, a man named John Wilkinson invented the machine that had an effectively revolving cylinder. In 1779, a man named George Medhurst then fabricated a compressor that runs on a motor.
Centuries then had passed, and men developed metal-piece, belts, and wheels. Engines were designed that further developed the constriction of air. Yet the most crucial innovative technology happened in the last fifty years. Yet its development is continuing until today because the world of commerce and industry demands it.
Knowing Basic Info
The rationale for the compression of air is not that complicated. It means if the air is compacted under extreme pressure, a good source of power is collected in a compartment, like a tank, until someone will need it. A good example: if you release a rubber balloon towards the wind, the pressure inside it is let out another kind of propellant (kinetic) energy.
In this process, the transference of kinetic energy is tapped to do particular tasks never been done before.
Air Displacement and Its Methods
The central principle of the compaction of air is best explained in two of its methods. To compact it, the inner portions of the compressor must allow itself to maneuver its position to drive the air via the compartment where constricting air and is stored for further use.
- A lot of the compressors utilize the technique named “positive displacement.” The air is forwarded into a compartment that shuts then opens continually, and then the inner parts cut down the mass within the compartment, thus compressing the air. As this cycle finishes, the air is pushed into a compartment for storage.
There are three kinds of compressors that use this technique: rotary-screw, scroll, and piston.
- This method is called “non-positive (or dynamic)” displacement. It is done by the use of fan-like blades to suck air into a compartment, where energy is collected and compressed from the rotating movement of the blades. It is usually partnered with turbo-compressors, which is mostly utilized in vehicles that have turbochargers.
The way this method of compression via turbocharging is that it lets out massive amounts of pressurized air at the same it, creating very forceful energy.
The usage for these techniques is used for commercial or industrial purposes wherein a massive volume of compacted air is needed.
Compressor Drives
It has two kinds of drives in the system:
- In a “belt-driven system”, the way it functions is that when a running motor revolves, so does the belt, thus enabling the pumping action within the system. If you are a person that wants to save money on this device, then this is the best one for you because it has an adjustable belt that can be altered due to the utilization of air.
- In a “direct-drive system”, within its crank-shaft, a motorized engine can be fastened that will enable lesser repair. Due to this drive-type, a design can be made tinier and portable. These are designed with efficiency in mind due to the minimal usage of power derived from the crank-shaft. Also, a few adjustments within the system are allowed.
A good thing about this type of system drive is its capability to give out pressurized air without filling the storage compartment first.
The Mechanics
The many kinds of air-pressurizing machines still follow the same basic course of action: First, an engine that has electrical power is needed. Then, a mechanism enables a pump to compress the air. It is then forced through an inlet and let outside through an outlet, which lastly, is collected in a tank.
To further illustrate it: Air is derived and directed into the device, then the inner components do the work of making a vacuum by bringing down the quantity of air, which cranks up the pressure and is directed to a tank for storage. Once the entire tank is contained air, the “duty cycle” is finished, and the device automatically closes.
The process mentioned above is different for compressors that utilized “positive displacement,” since they use scrolls, pistons, and screws within the system.
Piston Compressors
These kinds of compressors that employ pistons function the same way as a vehicle engine. As the rod of the crank-shaft takes the piston higher within the cylinder, the air is forced into the compression chamber, thus lowering the air mass and air pressure becomes higher. The crank-shaft then enables the piston to close and forces the air into the tank for storage. Then the piston opens again, the air gets pulled, and the cycle restarts.
These piston-based compressors can accomplish a full cycle of pressurization in either one or two stages:
- In the single-stage, the crank-shaft revolves only once to direct the piston in action. It means that the piston pressurizes the air in only one cycle.
- In the two-stage, the first part is the same as above, then the second stage is enabled as the compressed air is pushed through another cylinder for yet another cycle with another piston. The pressurized air stored in the tank is then doubled.
Loud sounds are emitted from these compressor-types, like with vehicles that have them in their engine. It is this way because the components scrape together and cause intense friction. Yet with new technology, these compressor-types have become quiet due to the addition to the system “dual and multi-piston.” By having this, instead of having just one piston, the compression work is divided into two or more, therefore minimizing sound.
Rotary-Screw Compressors
This type of compressor has two coil-like screws that rotate against each other but do not ever touch, this way it is easy to maintain and hardly makes a noise.
These are specially designed for heavy industrial uses that require lots of energy for long periods. Its purpose is ideal for factories that require mass production.
Due to its simplistic design, which has fewer moving components, they emit less noise and have lesser maintenance.
Scroll Compressor
This kind of compressor has become famous because of its effective functionality, its non-use of oil, and its soundless process of operation, the same as the abovementioned tool. The creation has two interconnected pieces that operate against each other without ever touching.
Two corkscrew-like pieces revolve around each other to pressurize the air. One-piece remains in place while the other connects inside it and moves without revolving in a circle movement.
Lubricating for Proper Movement
Its uses have many similarities with vehicles and the same as its usage of oil. It needs it to function evenly for longer periods.
The Lubrication process enables the use of oil to minimize wear and tear since the parts constantly rub against each other.
Similarly to piston-types, the application of the oil to the moving parts is done in two directions:
- “Splash lubrication” is done when the oil is dabbed towards the cylinder and the piston through a ladle-like piece that is connected to the piston rod.
- In the process of “pressure lubrication”, oil is directed into a pathway by a pump that has been set up within the compressor, thus the oil is implemented to different areas. This is the process of lubrication is costly, buy the direct current of oil keeps the functionality and operation in longer periods compared to the first one.
Compressors that do not use oil for lubrication are also known as “oil-free” or “oil-less” since their pieces are dabbed with particular kinds of substances similar to Teflon to minimize the friction instead of oil-based usage. Lubricating the parts permanently solves the problem of constant lubrication. The disadvantage is that they become heated quickly and not acceptable for industrial work.
Compressors that do not use oil are applied in companies where clean air is a requirement, like where electronics are manufactured, same with drinks and food. These devices are used by dentists because of their soundless and relatively clean functionality.
How to Calculate Power
When it comes to scrutinizing the flow and quantity of air within the device, there are two things professionals use as a basis for comparison to know if the device can deal with the application. Also to know the different kinds of instruments that work well with the device.
The implication of “pressure” in a compressor is the overall effect of force within it. The operation of force is calculated in PSI (pounds-force per square inch). If the PSI rating is above than usual, the force applied is also greater within the device.
The calculation of the “airflow volume” is the rate of movement of the pressurized air into the cylinder and how fast it pressurizes it. The amount of air within is calculated in CFM (cubic feet per minute). If the CFM is higher, the more air the device can provide.
The way to describe in terms laymen can understand when discussing volume and pressure is about water in a garden hose. If you put your finger in a portion of the opening, the flow of water is still the same but pressure is added via the finger on the hole. If the faucet is turned to full blast, the flow of water becomes stronger and more work with the hose is dome quicker.
New Compressor Applications
There was a time in the past where the compression technology was costly to make, with lots of power and energy employed to the maximum level, therefore enabling only for usage in large companies, not for personal use. Even during the current time, commercial compressor use still employs massive amounts of power.
Concerning monetary value, it will cost five hundred dollars per HP (horsepower) in one year for the continual application of this device for industrial usage.
Recently, in attempts to lower the cost, innovations were uncovered for its uses. Engineers and scientists are looking for ways to make this technology stronger and energy-saving. VSD (variable speed drives) and VFD (variable frequency drive) was discovered as a way to make engines more efficient and go faster and also save money and power.
The technology is still prospering, which will allow companies, industries, and people to make work faster that can also save lots of money.