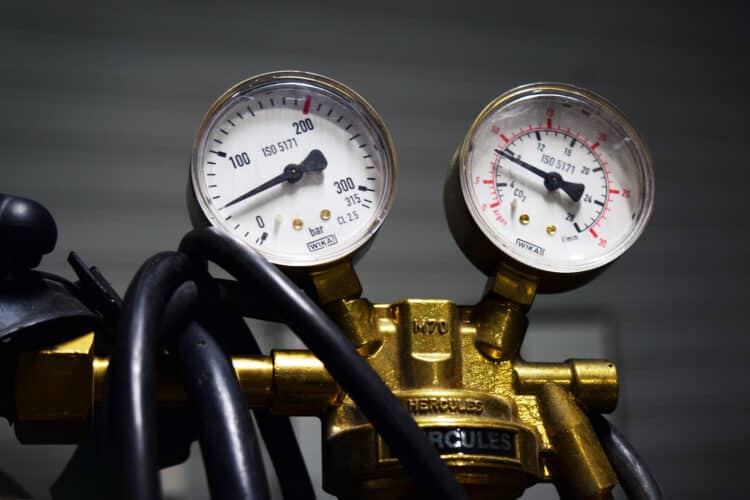
The overwhelming popularity of gas welding–particularly MIG and TIG welding machines–has prompted the development of different types and uses of gases over the past decades.
With over ten basic leading gases that can be combined to form new mixtures, choosing the right types of Welding Gases for your welding operations can seem confusing! There is no need to feel overwhelmed, though. Choosing the right gas is easy if you know the basics of the job you need to get done.
Let’s look into one of the most basic and essential components of the welding process, gases.
Table of Contents
Why is gas needed for welding?
Never underestimate the considerable contribution of gas in the welding process! Gas is useful in a variety of ways:
Gases are used to shield the welding arc from impurities such as air, dust, and other gases. These increase the risk of corrosion and the formation of weaker bonds.
Gas is also used to purge the underside of the seam opposite the arc of impurities
At times, the reactive gas is also used to heat metal.
Some gases are useful even after the welding process, effectively protecting the resultant weld.
What are the different types of gases used in welding?
There are two types of gases that are suitable for welding:
1. Inert gases
Inert gases are nonreactive even when exposed to a different set of conditions.
This means that inert gases do not change their properties or cause a change when in contact with different substances or temperatures. Inert gases are useful to achieve welds naturally without compromising strength and form/distortion.
Inert gases include but are not limited to noble gases. Noble gases (made of pure elements) are generally nonreactive in most conditions
Still, most other inert gases can also be in the form of compounds.
In special cases, inert gases can react to specific conditions, so it is important to carefully choose the gas used for welding.
2. Reactive gases
When exposed to specific conditions–such as contact with other elements and compounds or differences in temperature–reactive gases change their state or that of other substances. This is useful for welding when a state change in the weld or the welding conditions is needed.
Reactive gases can effectively enhance fusion by changing the process of the weld to favorable conditions.
How are gases useful in welding?
Let’s dive deeper into how gases are used in welding and how they can be useful for the welding process.
Generally, gases are used for the following purposes:
- Keeping the welding arc and the underside of the seam clear of impurities such as air, dust, dirt, and other gases
- Assisting arc stability and ensuring that metal is transferred properly during welding
- For protecting the resultant weld
- For heating
If gases are not used properly, you will get a porous weld or weak bonds.
Gases can also create a lot of spatter. This will make your weld much more difficult to clean and polish.
What are the different types of welding gases based on function?
To find out more about the correct type of welding gas you should use, familiarize yourself with the four types of welding gases based on their uses and function:
1. Shield Gas
Shielding gas is absolutely essential for MIG and TIG welding–both arc welding processes.
During the arc welding process, the air that gets into the welding arc will form air bubbles in the molten metal. Without a shielding gas, the weld will be unattractive and form weaker bonds.
Inert gases are ideal as shielding gases because they are able to maintain their properties and structure even under extreme and changing conditions. Inert gases are also able to improve metal fluidity and surface quality.
If the filler material is flux-coated or flux-cored in MIG and TIG welding, a shielding gas is unnecessary. This feature will serve the same purpose as a shielding gas by keeping impurities out of the welding arc.
2. Purging gas
A purging gas works similarly to shielding gas by keeping impurities away from the welding process. The only difference is that it works to clean or purge the underside of the weld instead of the weld pool.
While the top of the joint is being welded, purging gas is usually applied to the joint’s bottom to seal it off. You may choose to use the same type of gas as the shielding gas and purging gas, but it is equally acceptable if they are different.
3. Heating gas
Certain types of welding operations, such as gas welding and brazing, require the application of heat directly to the base metal or the filler metal to complete welding. This effectively removes the need for a welding arc. A heating gas should be reactive to effectively change conditions and temperature.
In many cases, the metal needs to pre-heated. The heating gas used for this is a mixture of fuel and air or oxygen, which is ignited by a fire source to heat or melt the metal.
4. Blanketing gas
A blanketing gas is used to protect the weld from contaminants and stains after the welding process. This is done by either filling-up a tank or a contained space with the blanketing gas to keep the air pure from other gases and reactions.
The finished weld may be placed in a tank of blanketing gas, or it may be placed in a confined space where the contaminated air and spaces are replaced with the blanketing gas.
What are the different types of gases used in welding?
Argon
Key features:
- Inert Noble gas
- Generally used as a shielding gas
- Safe and reliable gas for MIG and TIG welding
- Best gas for MIG welding
- Used in many air mixtures (including carbon dioxide, helium, and oxygen) to refine the welding process
Argon is the third most abundant gas on earth, making it a budget-friendly option. It is one of the most commonly used inert noble gases in welding. Since it is inert, it will generally react with other substances.
However, it was found to change under extremely high temperatures.
Applications and Uses
Argon is the number one choice as a shielding gas to protect the welding arc from dirt and other air contaminants. It is generally used in the primary welding stage, but it is also useful as a purging gas.
Why is argon suitable for welding? It can be used both in its elemental state, and it is also commonly used as a mixture.
Argon is considered the best gas to use for MIG welding and TIG welding.
Carbon Dioxide
Key features:
- Generally used as a shielding gas
- Cheaper alternative than argon as a shielding gas
- The product is of lower quality, and more spatter produced compared to the use of argon as shielding gas
- More commonly used in gas mixtures to improve quality
- Its pure form may be used for flux-core welding, plasma shielding, and MIG welding of carbon steel
Carbon dioxide is also one of the most abundant gases found in the earth’s atmosphere–it is in the air we exhale. It is a by-product of the decomposition of organic matter.
It is easily produced on an industrial scale, making it even more affordable than argon though the quality is compromised.
Applications and Uses
You might be wondering which is better, Argon vs. CO2? Welding with CO2 is the cheaper alternative to argon as a shielding gas. Still, it does not produce the same quality as argon, and spatter is much more pronounced. Since this is the case, carbon dioxide is more commonly used in mixtures rather than alone.
In its pure form, carbon dioxide may be used in flux core welding, plasma shielding, and some cases of carbon steel MIG welding.
Helium
Key Features:
- Does not freeze
- Used as a shielding gas in pure form or in mixtures
- Used as a heating gas
- Argon mixture is suitable for welding aluminum and TIG welding
Helium has a unique property: it shifts from the gaseous state to the liquid state without ever becoming solid. Even at a temperature of 450 degrees Fahrenheit, helium will not freeze and turn into a liquid.
Helium is a limited element and quite expensive compared to other welding gases.
It is also widely used in rockets, scientific experiments, decorative and technical balloons, and hypersonic wind tunnels.
Applications and Uses
Helium is used as a shielding gas in its pure form and in mixtures.
It can be used in both MIG and TIG welding as an effective shielding gas. It is able to penetrate deep into weld arc, and is able to increase heat into the weld.
A concerning issue, though, is that it is difficult to get a consistent arc start. The solution to this is to combine it with argon–known for extremely consistent arc starts.
The combination of argon’s consistent arc start and helium’s heating properties makes it suitable for welding aluminum and TIG welding.
Compressed air
Key features:
- Cheapest gas available
- Compression into a tank allows a great volume of compressed air to be released with high pressure
- Used as effective heating gas
- A convenient and effective way to blow contaminants away from the worksite
Compressed air is literally the air we breathe in, but in compressed form, usually in a tank. Compressed air is a mixture of 78% nitrogen, 21% oxygen, and 1% other gases.
A massive volume of air can fit in a small tank, creating significant amounts of pressure in the process. When compressed air is released, the pressure which is consequently released aids welding applications.
Applications and Uses
Compressed air is not usually used in the actual welding process as it contaminates the weld. Though this is the case, it still offers many functions around a welding workshop.
Compressed air can be used to effectively blow away dust, swarf, and other dry particles and debris around the workshop. This is done by attaching air nozzles with hoses to the compressor.
When compressed air is mixed with a fuel, an intense flame with a lower temperature than an oxy-fueled flame is produced. This is a convenient and cheap way to pre-heat metal right before welding.
Compressed air ensures an even transfer of heat and has a low transition from cold to hot. These are necessary for the welding process of certain materials, such as carbon steel.
Compressed air allows welders greater control of the thickness of carbon coating.
Oxygen
Key Features:
- Highly reactive gas
- Improves the fluidity of molten metal when mixed with a shielding gas
- Can speed-up the welding process
- Effective as heating gas
- Mixture with acetylene produces the only flame hot enough to weld steel
- Best gas mixture to weld stainless steel
Almost all forms of life depend on oxygen. It is odorless, colorless, tasteless, and highly reactive. It can be combined with almost any other gas except the inert gases.
Applications and Uses
For effective use in welding, oxygen is generally mixed with other shielding gases to improve the fluidity of molten metal and to speed up the reactions in the welding process.
Oxygen is also useful for increasing the temperature of gases with fuel and oxy-cutting metals. When mixed with acetylene, it can produce the only flame that is hot enough to weld steel.
Oxygen is also useful in gas welding as an alternative shielding gas for metals that require a flux filler wire.
Nitrogen
Key Features
- Used as a shielding gas in pure form or in mixtures
- It can be used for some heat treatments
- Improves mechanical properties of nitrogen-rich alloys and enhances penetration
- Effective and cheap as blanketing gas
Nitrogen is the most abundant natural gas in our atmosphere. It is an essential component of every living organism.
Nitrogen is also useful in preserving and protecting products such as food, motor, tanks, and anything at risk from contamination from oxygen and other gases.
Applications and Uses
Nitrogen can be used in its pure form as a shielding gas for laser welding and plasma cutting, and it can also be used for some heat treatments. It can also be combined with other shielding gases for special applications, except for carbon steel.
When nitrogen is used as a shielding gas for nitrogen-rich metals, it is able to improve the mechanical properties of the alloy. It can enhance penetration while stabilizing the welding arc.
Nitrogen is also useful as a blanketing gas.
Since nitrogen is abundant, it is also very cheap in large amounts, which makes filling a large contained space much more affordable.
Hydrogen
Key Features:
- Highly reactive
- Used as a shielding gas in mixtures only in small amounts
- Effective as a heating gas
Though a simple element and reactive, hydrogen is effective as shielding gas.
Since hydrogen is highly reactive, it is only added in small amounts and can effectively increase temperatures.
Applications and Uses
Hydrogen is commonly used as a shielding gas in mixtures with argon or carbon dioxide.
A specialized welding process called “atomic hydrogen welding” uses 100% pure hydrogen and to produce an arc heat range up to 7200 degrees Fahrenheit. This allows the welding of materials with extremely high melting points, such as tungsten.
Many people would think that including hydrogen in mixtures is unsafe. Since it is only generally added in small amounts, the process is very safe.
Precautionary measures can solve these risks. Weld cracks may appear when hydrogen is used as a shielding gas, but it can be avoided by adding protective layers.
Hydrogen is an excellent choice as a shielding gas due to its reactive properties that generate incredible heat levels. This enhances penetration, which makes for one of the cleanest gas welds.
What gases are best for oxy-fuel welding?
The three most common gases used for oxy-fuel welding are acetylene, propane, and propylene–all extremely flammable gases.
Acetylene
This gas is highly flammable and highly combustible in air. It is used widely in the production of chemicals and industrial purposes.
When mixed with oxygen, it is the most effective gas to create a fuel source. The flame produced is hot enough to weld and cut most metals.
It is more expensive than other gases, but it is one of the most effective.
Propane
This gas is highly flammable and highly combustible in air. Propane is commonly known as LPG or Liquid Petroleum Gas, a reliable fuel source.
Unlike acetylene, propane cannot be used directly in gas welding as it does not create a reduction zone. Otherwise, it is effective for brazing after welding is complete.
Propylene
Propylene is not a pure gas, but a blend of oxygen. It can create higher heat levels than propane and O2. It is best suitable for specialized forms of welding, heating, and brazing.
What are the different types of mixed gases used in welding?
Each welding gas has unique properties that allow them to excel for certain applications while also lacking in other areas.
Mixing gases with different properties to find the right balance is the perfect way to compensate for these lacking properties.
Some of the most common mixtures are:
Argon and Oxygen
The oxygen content of this mixture is minimal. Otherwise, the metal would burn too hot.
This mixture is normally used for welding light gauge steel to enhance material fusion.
Oxygen is minimal to prevent damage to thin and fine material.
Argon and Carbon Dioxide
This mixture is often used as an effective shielding agent that results in a smooth surface and minimal spatter. It is the most common gas used by welders because it is inexpensive, and it gives great results under most conditions.
The components usually range between 80-95% Argon and 5-20% CO2. The percentage for carbon dioxide needs to be higher the thicker the metal.
Argon, Carbon Dioxide, and Oxygen
If you’d like to improve fluidity to the argon and carbon dioxide mixture, adding oxygen is the effective solution. Oxygen can also make the welding process more efficient and productive.
Argon and Helium
This argon mixture is the best choice for welding aluminum and alloys. The mixture enhances penetration and features a wide-finish on the weld.
Argon, Carbon Dioxide, and Helium
This mixture can be customized specifically for your welding needs. Some mixtures will have more helium, while some will have more argon.
The versatility of these mixtures makes them suitable for a variety of materials, such as stainless steel, carbon steel, and aluminum.
Argon and Hydrogen
This mixture effectively accelerates TIG welding operations while enhancing weld cleanliness. Hydrogen acts as an effective shielding gas to prevent contamination and oxygenation.
Nitrogen and Hydrogen
This mixture is for specialized use in the welding of austenitic stainless steel.
The combination of these two gases enhances penetration, which accelerates the welding process. It also enhances the mechanical properties of the stainless steel product.
How are Laser Gases used in welding?
The laser processing industry relies on strict standards for welding gases.
These usually contain helium, nitrogen, carbon dioxide, and carbon monoxide.
The main purpose of these welding gases is to reduce the number of contaminants that might enter the laser system.
The presence of contaminants in the laser system considerably reduces the machine’s efficiency and increases repair costs due to damage.
What other factors should you consider when choosing a welding gas?
Aside from the type of gas you should use, ensure that your supplier has reliable storage and piping systems in place.
This will ensure that you receive a gas that is free from contaminants that may otherwise compromise the quality of your welds.
How are welding gases stored?
It is equally important to give attention to the type of supply system. This will have a considerable impact on the overall purity and quality of gas.
Pure Gas Supply
Compressed-gas cylinders: Need regular refills, which makes this system vulnerable to contamination. A useful feature is to have a built-in purity check on the valve that will detect gas impurities.
Liquid cylinders: Also called dewars or VGL, these systems offer more quality control.
Bulk Liquid Gases: This system offers a high purity level since it is transferred directly from the production site to the buyer’s on-site storage.
Tube Storage system: These systems can be trailer-mounted, skid, or ground-mounted. These systems are also regularly refilled, increasing the probability of impurities.
Mixed Gas Supply
Many shielding gases are supplied in cylinders or a similar storage system (based on quality and quantity ordered). Switchover manifolds and compressed shielding gases can reduce the risk of contamination.
Piping
Make sure that the piping system is up-to-date and reliable. Contamination can easily occur, especially in metal arc welding operations.
Gas Safety
Welding operations entail exposure to different kinds of welding gases. Make sure to keep in mind these safety precautions:
Flammability
While most gases are inflammable, any other flammable gas near the worksite should be treated with extreme caution, especially acetylene. When not in use, safely store away flammable gases. Keep them away from the welding machine when not in use.
It is a responsible practice to keep a class B fire extinguisher during welding operations.
Ventilation
If you are working in a confined space, make sure that the working area has proper ventilation. Some inert gases may cause asphyxiation when inhaled.
Make sure that your worksite has gas detectors, a spotter, and some extractor fans. Take regular breaks to reduce the inhalation of toxic fumes.
Gas Tank Care
Tanks are designed to be durable and withstand constant impact, but it will still be best to handle them with care. Be especially careful of the valve at the top of the tank.
Conclusion
Successful welding operations rely on the proper use of welding gases.
While there are many options, it is incredibly critical that you familiarize yourself with the different gases and their specific purposes.
Some gases function well for many different purposes, such as pure argon for most TIG welding jobs and a mixture of argon and carbon dioxide for MIG welding.
Each of these different gases and mixtures will have its own strengths, and to get the best welding result, you should learn to maximize these.