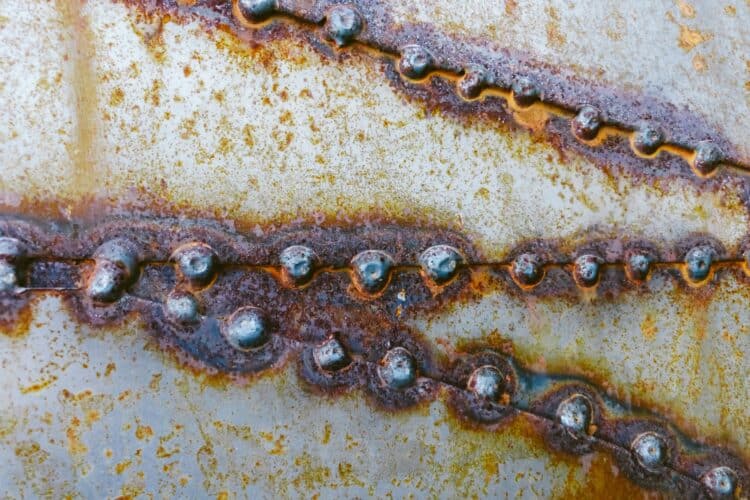
For newbies, the first kind of weld you start making is known as a bead. A weld bead is a welding seam deposit created during a single welding procedure. So long as you are wearing the correct welding helmet, you can combine various weld beads when welding.
How do you create a weld bead? You form beads when you use a filler metal to deposit them into a joint between two pieces of metal. When melting a filler material into a metal, how you move the torch affects the puddle advances. It also affects the type of bead you leave in the joint.
A welding bead might be narrow or broad based on the oscillating movements the welder uses. A grooved seam can be bonded with one or more welding beads depending on the thickness of the metal. Welding seams can also be conducted with many passes through the layer. You can do this by dropping at least two beans in the groove.
Check if the molten material melts together and if a rod or wire is added to a welding rod. This creates extra material for the joints during welding. The rod melts into a melted puddle and requires a closer and closer movement of the rest of the rod to sustain the arc. You should stop soldering if you use the rod and you end up having only a few inches of flux coating the holder.
Keep in mind that the rest of the butt of the old pole is superheated. So a lot of care needs to be taken, and understand that it is just a tiny piece of material. The goal is to fuse the surface with a flat soldering bead on the bottom. The seedlings bar welder is the initial soldering process conducted through the root-pass.
Table of Contents
Why is it necessary to use different torch movements?
There are several techniques to run a welding bead along a metal seam, like stitching a seam into cloth. Welders often have to execute in a difficult position with a face shield and gloves. This is different from what the welders do.
The force of gravity also contributes. It affects the deposition of molten metal between metal plates or sections of a pipe. For example, you must move fast if you’re welding overhead. If you don’t, the molten metal drops on your facial shield rather than filling the joint.
As a welder, you must use a specific stroke and move it. It is the immediate step a welder must take after making preparations for joint welding. Next, you should pick the correct filler material. The right wire, rod, and stick and the correct machine settings are all critical.
Types of torch movements and weld beads
It does not matter what you supply the welding pools with. Whether it is a separate rod, a stick electrode, or the manually fed wire. The torch movement will be the same. But, some approaches are applicable in one process.
We have four main types of torch movements that one can use to create weld beads. Let us have a rundown on the torch movement types below:
Stringer beads
A stringer bead is a simple method where you either draw the torch (drag) or pull it across in a straight line. This should not move or reduce side-to-side.
Drag means that the electrode is inclined towards the “ahead” solder. In the process, driving the puddle. It allows maximal penetration and sturdy welding.
The welders “push” onto the end of the torch. It is important to do so for thin or heat-sensitive metals or vertical soldering. You must remove the puddle from your torch and follow it as you weld it.
The molten metal likes to sink when welded on a vertical joint. But, pressing the solder takes the heat away from the puddle. thus, it lets the solder crystallize fast.
One of the disadvantages is that the base metal penetrates less than that of the molten puddle. On the other hand, one of the advantages of stringer beads is that they are not broad. Thus, they apply in many welding positions.
Even if you go straight, it’s still vital to “step in” on each side of the joint with the solder toe. Note that the purpose of soldering is not only to fill a joint with new molten metal. Fusion from the weld to the base metal is crucial.
The liquid sometimes flows across both sides of the joint by moving the flame slowly enough. It can be everything you need to produce a successful fusion. In other instances, as demonstrated below, some side-to-side adjustment is required.
As you continue with the movement, ensure that the side-to-side manipulation is slight. Please also note that stringer beads are helpful in hard-facing. It is a surfacing procedure that increases the durability of industrial devices. It also improves the simplicity of scoops, slabs, plows, and other external elements. In this case, the beads do not fuse with the base metal but produce a protective layer.
Weave Beads
You can weave from side to side along the joints if you want to work with wide welds. Weaving is the fastest approach to complete a soldering task for a big joint. For instance, weave beads are the best if you need to do groove welds on thick welds. You can also expect to find weave beads on fillet welds.
There are, of course, weaves of all kinds, and every welder has their favorite. You can do a zigzag, crescent, or curlycue motion.
Apart from covering a wider bead, the weaving of your weld puddle does the work of heat management. You can also pause on either side of the weld to get a good connection to the metal parts and not undercut the edges.
But you will want to rush when you travel over the middle of the joint. Otherwise, a tall crown may appear. You are likely to see a bulge in the middle. So, instead of the tall coronet or the swell when you weave, it is preferable to end up with a flat or convex weld face.
When filling a deep hole, a triangle weave is crucial. This approach allows you to build a rack behind the puddle in vertical-up welding. The approach prevents the molten metal from flowing down.
A semi-circle weave with the stroke crossing the front of the puddle or the central point can be crucial. It can prevent expansion or overheating. If you want additional heat in the splash, weave the crescent back through the spill.
Overhead weaving is demanding. Gravity tends to interfere with the position and direction of the molten metal from the weld. Even welders with experience can find it challenging doing an overhead weave bead. It should not be wider than half-inch. But, welders learn to do this because weaving saves time compared to several string beads.
Stick Weld Beads
Stick welds can have a wide range of bead properties. Stick welding procedures are useful. They can mean the difference between a nice stick and an unattractive gold weld.
The low hydrogen rod family is quite flexible. We could employ standard hydrogen rods that come with a depressed hydrogen rod. Draw a straight bead with ease using these beads.
Furthermore, these stick welding beads are significantly narrower than others. Because they are even and constricted, they are called “stringer” beads. Vertical welding is preferable with a weave pattern. As a result, the welder can distribute the filler, molten metal on the alloy plates in many designs.
The welder should be skilled at creating an arc while keeping the rod in place. Doing this is critical because it helps form a shape that looks like a coin using this technique.
The first weld undertaking of the welder is to carry out a whipping motion with their wrist on the root pass. The goal is to join the work plates at the bottom with a flat bead of weld metal.
E6010 and 6011 fast-freeze rods seem to be the most often used stick electrodes. They are mostly used for root pass on low-carbon steel.
The work of the welder is to move the electrode through and along the gap. It’s critical for fruitful entrance. Consequently, a keyhole will appear in the aperture at the puddle’s head.
The Stick technique is one of the most challenging techniques for a welder to master. One thing is that a welder has to maintain the keyhole size and watch the puddle simultaneously. Should the size get broader than the keyhole size then it becomes hard to join them. It’s why heating containment is so critical throughout a root pass.
Appropriate joint design and welder settings allow one to take charge of the size of the keyhole. Use the timing of your whiplash strokes.
The welder must whip the rod slightly upward and above the weld. Please bear in mind that this must get done before the keyhole expands excessively. It also makes it possible to tighten the bead at the back of the puddle.
You whip back to the molten pool immediately after the bead solidifies. And a further drop of the soldering material should come off your rod. Be careful because all this could happen very fast. Also, note that the heat levels you see in the weld determine the whipping pace.
You may not be whipping at all when you commence a weld first because heat is not adequate at this time. After the weld, the heat flowing through the base metal will allow you to flicker the handle at a steady clip.
The J-Weave whip variation
The j-wave is a version of whip movement. It combines whip and the crescent whips strokes. It is also employed mainly on the second pass of the V-groove joint. It is also called HOT.
Slide the E6010 or other rapid-freeze electrodes from one toe to the other. This to occasionally stop on either side and then whip the rod forward and upward along one side of the joint. This should be for a few seconds.
A lengthier arc is advantageous for this operation. And, much like on a root pass, after whipping forward, you’ll whip back to the next spot available. Do this on the weld’s left (or right) toe and continue the stroke.
Walking The Cup (For TIG)
Accuracy and quality typically take priority over speed in any pipe welding application. Just like MIG, TIG is a form of arc welding.
The “walking the cup” technique is suitable for pipe welding. But, there are a few more situations where walking the cup might produce a better-looking weld. When the cup is resting in a groove or between the two sides of a tee joint. Or, when the cup is resting on the exterior of a pipe or a flat surface.
The continual motion needed to keep a steady arc length is challenging. Also, the dab filler metal in the weld puddle can be exhausting and irritating to maintain motion. Adjusting angles on the fly to accommodate the welding motion on the pipe is challenging. To produce quality welds under these conditions, the welder must devote a lot of time and skill.
TIG welds are some of the prettiest welds you can produce. TIG welds look like dimes that are stack together. It is due to the welder’s other hand providing filler metal dabs that are spaced uniformly while the arch of the TIG moves.. When you lay these dabs on top of one another, they form a rounded shape. The placement of the dabs influences how the weld looks. Should you be fast in feeding your filler metal,, it will result in closer dimes spacing and vice versa.
The cup walking technique is broad. As such, it demands the welder to have a substantial amount of experience and expertise.
TIG welds may not always exhibit the appearance of arranged dimes. At this point, the welder has to hold the filler wire and lay it on the fused metal piece.
The welder needs to move with the TIG plate back and forth as they advance through the weld. The filler rod is then heated and melted before being distributed around the weld joint. It’s similar to spreading cream cheese on toast. This is the preferred method among tubing welding professionals. You can use up to three filler rods at the same time. This is done to increase the amount of filler deposited. Think about moving the cup as “twisting” as opposed to a straight weld.
When you should not use walking the cup technique
Not all jobs are suitable for this technique. Machined parts with a smooth finish are not appropriate for this technique. For example, you will realize that many people hate the scratches on the ceramic cups. This is obvious if if you have done a lot of welding for machine jobs. Walking the cup may be good on pipes; however, you will start having problems when you get to 2 inches pipe or lower. When it does get this narrow, a better alternative would be to use a free hand. Most welders claim that freehand is best for pipes that are at most an inch wide. Remember to use a tig finger when you decide to use a freehand technique.
Summing-up
The first form of weld that beginners learn to produce is known as a bead. A weld bead is a weld joint deposition created during a welding process in a single operation. Welds with beads can also be a combination of steel rods and dowels. The come with various kinds of beads in them, as long as the welder is wearing the proper welding headgear. The welder produces an arc and holds the rod in place to form a “coin” in this procedure. It was created to improve the hardness of the parent metal’s HAZ and to weld other metals.
With current flowing through the weld, a single generator can produce at least two welds at once. Thus, this results in a completed product that looks like an oven. A single transformer can produce more than two welds at once. The total current must flow through the weld
This results in a final piece that looks like an overlapped coin or arc. A welding bead seems to be a circular deposit in cross-sections. However, a welder may need to make numerous welding beads to properly seal the 2 filler materials. The welder holds the electrode at a 45° to 90 ° angle while laying a soldering bead. Welders can enhance their technique by producing woven beads of varying widths. They can use transverse vibrations. Weaving beads is just what it sounds like. Yet, a bad weaving technique might cause the undercutting of the bead.
Filling a joint with filler materials is largely dependent on the movement of your torch. Especially one with larger joints. Recognizing the different approaches will allow you to improve weld’s quality
You adequately prepare your joint. You must also select the correct filler materials and set up the welding procedure. Finally, you must ensure that you settle for the appropriate torch movement. It will depend on the type of bead you want to produce.