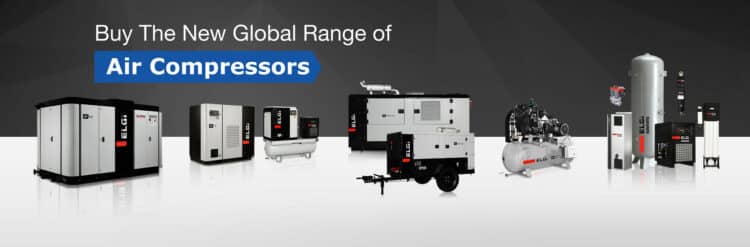
If you are a serious hobbyist and want to upgrade your workshop to the next level, your next logical step should be to acquire an air compressor. It is an essential tool that you can use for all sorts of tasks, some of which you might haven’t known before. Yet you do not know anything about it and want to learn more.
To gently ease you into this particular subject matter, you should learn about air compressors, belt-driven, direct drive, and which is more superior. Their fabrication and operational processes are not complicated to find out and take to heart.
Table of Contents
How does an air compressor function?
Before going through the nitty-gritty, you should first learn about the general functionality of a typical air compressor unit. And how it relates to its many types and subtypes.
Its chief purpose is to change electrical power to compressed air. Whenever air is pressurized, it becomes more powerful. Thus, making it practicable for many different kinds of applications, whether in workshops or large industrial complexes.
Inside the device, there is a storage of compressed air. The pressurization creates raw power, which can be used to make pneumatic tools work.
It continually operates by absorbing, circulating, and filtering the air. Then it is put back to the outlet at the correct compression.
Its types are usually available is in small and compact sizes and only need a small motor to function. Some are portable and mobile, make less noise, and very durable. Almost all types are supplied with power from gas engines or electric motors.
Main compressor components
A basic compressor unit has these:
- Drive- There are two kinds of drives in a typical unit: direct driven and belt-drive (which will be explained in detail in corresponding sections below)
- Pump- The energy created from the drive is used by a pump to draw in and pressurize the air. It is then directed to tubing and ends up in a storage tank.
- Storage tank- Its main function is to temporarily store the air, which you can then use for all sorts of operations while it is still not functioning. It also provides extra air to the system throughout periods of constant usage.
It is outfitted with a one-way check valve to halt pressurized air from adding compression to the pump. It acts as a buffer that does away with any potential wear and tears happening to the motor and pump for constantly operating.
Compressors’ life expectancy
One of your aims in buying an air compressor, or anything for that matter, is to get something reasonably inexpensive yet very durable and has the potential to last long.
Yet, some compressor brands are advertised and made to last ten times longer than the others of their type. Then you find out there is only a little difference in the pricing. It makes potential buyers like you more confused.
The compressor’s life expectancy should be discussed by your dealer before purchase. If he has no inkling, then have him call its manufacturer.
As a principle, for every dollar you pay out to acquire a better unit, you ought to saves about three dollars in the longs haul.
Apart from buying a top-quality unit to get a longer lifespan, you get a larger compressor instead. A bigger one can function two-thirds more than smaller ones and remain cooler and last two times longer.
Overview of air compressors belt driven and direct drive
The first crucial step is to learn about the distinction between a direct drive vs. belt drive compressor unit. Knowing all the facts and how to use them will get the most out of their performances in providing power to pneumatic tools. And also, in the long run, save money and energy.
A belt-driven air compressor and a directly driven air compressor come from one type, which you might have heard before: a rotary screw compressor.
What is a rotary screw compressor?
It is also known as a twin-screw compressor.
It is a particular kind of gas compressor that utilizes a kind of rotary positive displacement mechanical part, known as rotary screw air end.
They are used mostly in large industries to substitute piston compressors, wherein a massive quantity of highly compressed air is required. A great example to illustrate its functionalities is the usage of commercial chillers. Or operating air-powered tools like impact wrenches or drills.
Its pressurization process is unlike that of a reciprocating piston compressor. The rotary screw air end mechanism produces air pressurization in a continual forward motion. There are only minimal pulsing and flow surges that usually happen with piston units.
Rotary screw units have two coil-shaped screws that are interlaced with each other. These are utilized to pressurize the air and are known as rotors.
Factors to consider
When you are at the stage where you have to make up your mind between the two, here are some elements you need to think about first:
- Starting cost
- Adaptability of speed and pressure
- Environment
- Duration and frequency of usage
- Maintenance
- Efficient in dealing with energy
- PSI or pounds per square inch, CFM or cubic feet per minute, HP horsepower, RPM or revolutions per minute
All of them can enormously affect the safety and performance of the unit itself and the air-powered tools since each has different pressure demands and output.
Either of which you will end up selecting has different positive and negative attributes, which can aid in your decision-making process.
What is a belt drive air compressor?
It simply got its name from the belt linked to the motor. Whenever the motor functions, the belt propels the pump to the pulleys. The pulleys’ diameters regulate the PSI and speed of the unit.
Advantages of a belt drive
Since you need the right compressor unit that fits your DIY proclivities, the belt-driven one might be the right one for you. It perfectly suits a small-scale, one-man indoor workshop that has a few work areas.
- Noise level- This compressor type operates efficiently and quietly due to an oiled belt system. It is ideal for home use and would not serve as a disturbance in the neighborhood.
- Uncomplicated maintenance- Once you purchase this unit, there will be no complications since installing it will be straightforward and minimum resources will be utilized.
Maintaining it will be fairly simple and only necessitates lubrication and once a month belt stress testing. It is also recommended that you substitute the filter and oil every five hundred to one thousand hours of usage. - Flexibility- If you intend to use it sporadically at varying power and speeds, you will likely favor the flexible nature of this belt-driven unit. You can easily go to the manufacturer settings and alter the pressure.
The most high-powered pneumatic tool needs one hundred PSI. However, this compressor type can only function at ninety PSI. If you want to increase it, you have to substitute the pulley system.
Disadvantages of belt drive
Even though this compressor type might look good on paper, there are still negative aspects, but only minimal and would not be a hindrance to you.
- Belt weathering- The belt being worn out due to constant usage is its biggest issue. It can result in getting severed in half, so replace it before it happens.
- Environmental sensitivity- This compressor type cannot endure in a severe environment that has intense temperatures. It should not be situated in an area that either has below zero Celsius or higher than 40.5 Celsius.
- Belt tension and not properly aligned pulleys- The belt and the pulley system are two of the most crucial components of this type of unit. So you have to regularly examine the pulley alignment and the tensile strength of the belt.
Not being correctly aligned can induce the motor function to add too little or too much pressure and might overload, which in turn, makes the belt malfunction.
What is a direct drive air compressor?
The main difference of this directly driven compressor type is that they are no intermediary links between the belt and the pulley system. Instead, it has a crankshaft joined straightaway to the motor.
Advantages of a direct drive compressor
This compressor type is the best choice for professionals working in a large factory or plant because not much energy is consumed during operations, thus saving company funds.
This energy-saving attribute makes it an economical and ideal alternative for heavy machinery and equipment like high-powered jackhammers.
- Few components mean few replacements- Compared to its belt-driven counterpart, it has not many parts that move. So there would be less maintenance work to do and can save on the cost of replacement parts.
Since this type does not employ a pulley system, there would not be constant lubrication except for the occasional change oils and top-ups every week.
Changing the compressor oil should be done every one hundred to five hundred hours, which will depend on the oil type. - High tolerance for severe conditions- If you live and work in a place that is environmentally intense and has a climate in the extremes, this unit is particularly tough to withstand.
It can resist the coldest of temperatures below freezing levels and the hottest of weather from up to forty degrees Celsius. Experts recommend the usage of synthetic oils during the hot or freezing seasons since their attributes will not change in those conditions.
Disadvantages of direct drive
Even though the outlet pressure can be modified to one or two bars, this compressor type is not as flexible as its belt-driven counterpart. Since a pulley system is not present in its assembly, the speed and pressure cannot be regulated.
Its maximum PSI is one hundred and eighteen. If you need more than that to power your pneumatic tool, there is no way to increase it.
- Noise level- Loud and irritating sounds are never good in a small workshop or a massive industrial space. If you require a tranquil and quiet work environment with your pneumatic tools, this type of unit would not work for you.
Its crankshaft is not connected to the motor, and for this reason, it does not function as swimmingly as the oiled belt-driven unit. The high level of noise it emits would not be ideal and will likely disturb a neighborhood area. - Complicated and costly repairs- The unit’s entire mechanism for the motor and crankshaft connection make fixing complex and expensive if they happen. Whenever the motor malfunctions, it can also inflict harm to its connected components.
An example of an expensive and long fix is oil loss resulting in damage to the shaft end seal and gearbox. - High price- If you are looking to find the cheapest compressor around that provides the most pressure, this type is not the one you need. The starting cost is quite expensive for a DIY hobbyist that only uses it intermittently and will not be worthwhile in the long run.
It is why large industries use it because the high price will be an investment for them, and can get the cost back after constant usage.
Safety and performance
It is essential to think about safety and performance when selecting the type of compressor to purchase. If you choose one that does not provide the right PSI capacity for your air-powered equipment, it can become damaged or cause injury to yourself and others.
It can also cause a massive impact on your energy costs, personal workload, and general wellbeing. Knowing everything about them is truly necessary and will invariably assist you in the long run.
Conclusion
Now you have learned everything there is about air compressors, rotary screws, belt drives, etc. As a serious hobbyist looking for the best compressor for your workshop, have you decided on the one that corresponds to your needs?
The best one that fits your particular proclivities would no doubt be the belt-driven one. It has enough energy to power your pneumatic tools, won’t take up a lot of space, and importantly, does not make a lot of noise that can bother your neighbors.
This compressor type can get you more bang for your buck.