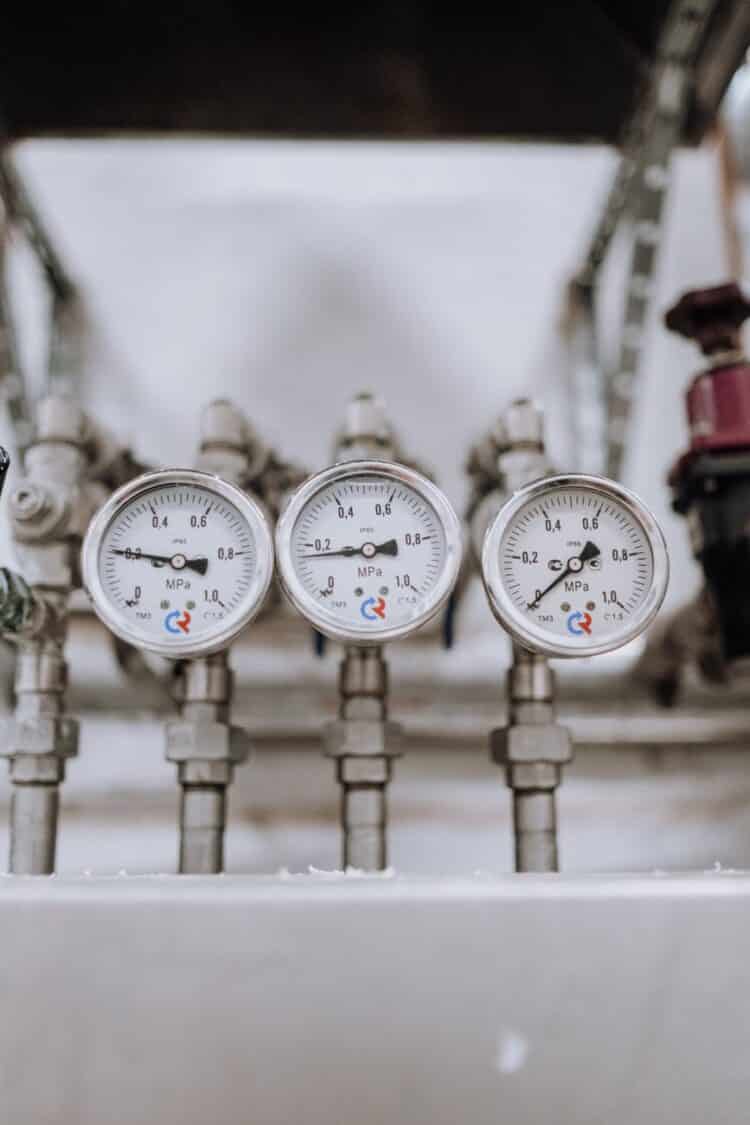
Compressed air units are versatile and convenient pieces of equipment. They have several applications, so it makes sense to own one. What does not make much sense is to have an air compressor and now know how to use it well. It is the responsibility of persons who have air compressors to understand how they work. Using them is simple once you get the hang of the process, but it is not as easy as plugging in your tools. For example, not all pneumatic workshop instruments function using the same amount of pressure. Some need more. Others need less. And if you want your air-powered tools to do the job they are supposed to, you must get the pressure setting right. Our article will teach you how to adjust air compressor pressure regulator for your air-powered tools.
Table of Contents
How Does A Pressurized Air Tank Work?
The most obvious task of your compressed air unit is storing potential energy in its pressurized receiver tank. That tank will hold as much as the tank will allow under extremely high pressure. The tank will stop compressing the air in the tank once it reaches capacity.
The highly pressurized air is what we need for air-powered tools to function. As soon as you start using that compressed air, the pressure in the tank begins to drop. When the drop in the air pressure hits the lowest point, the process starts again. The compressed air unit sucks in more air for pressurization. A monitor will let you know the level of pressure the air in the tank has.
If your compressed air unit is on the large side, you may notice that it has a number of regulators. With these added features, you can use compressed air to complete a number of jobs at once. All you have to do is remember to adjust each regulator based on the needs of the application tools.
What Parts Makeup Pressure Regulators?
You want to know how to adjust air compressor pressure regulator. But to learn how this works, you must understand how a compressed air regulator functions. The first place to start is with the parts that make up this instrument.
The components that make up pressure regulators are the ones that control the airflow to and from your equipment.
Below you can find a list of the elements that help air compressor pressure regulators do the job they were designed to do.
- A pressure-reducing element
An example of pressure-reducing elements in pressure regulators are poppet valves. This valve controls the quantity and timing of the flow of air from the compressor to the tool. - A loading element
Loading elements come in different forms. They can be springs, diaphragms actuators, or piston actuators. These devices cause the element for sensing to release a valve. The level of spring force varies and will determine how much out pressure flows out of your equipment. - An element for sensing
Sensors on pressure regulators can be a diaphragm or a piston. The kind with the diaphragm offers better accuracy. They have lower levels of friction than the piston designs. That’s because of the elastomer used to make them. It is a thin material with higher sensitivity to detect pressure changes. They also have a wider sensing area for specific regulator sizes. For this reason, this type of sensor is better for less high-pressured applications.
Pistons can be sluggish because of friction between the regulator’s body and the sealing. That is why they work better under high-pressure applications. The extreme pressure will force them to push past the friction.
How Do Pressure Regulators Work?
What controls the air flowing through the receiver tanks of compressed air units are large set screws. It maintains the pressure in the air using some springs.
Why Should You Adjust Your Compressed Air Unit
Pressure regulator are necessary components of compressed air units.
When using air compressors, your project’s success depends on your ability to operate the equipment. Setting your compressed air unit’s pressure regular to fit the requirements of your pneumatic tool is of utmost importance if you want a job well done.
It controls the force of the air as it passes in your system. If there is no regulator on air compressors, then users have no way to control the intensity or pressure of the air flow from the receiver tank into their air-powered tools.
The job of pressure regulators is to protect each tool from the effects of air that is too powerful. It also ensures that you do not under-power these tools, which can affect the quality of the work. Rressure regulators ensure that your tools function smoothly and that you are happy with the job you do.
Regulating your compressed air unit serves other functions as well. It reduces the amount of energy your use to drive air-powered tools. If you choose not use this device, you might consume more energy than your applications need. You will end up spending high levels of energy on one job using the amount of energy it takes to run several of your pneumatic tools. Adjust the pressure takes up less energy and will save you money on your electricity bill.
The last reason adjusting your system’s pressure regulator is streamlining. Every time your receiver tank runs out of your, the process of pressurizing starts all over again. Regulating the air pressure to fit the tools you use will lessen the frequency of those cycles. The result will be an increased life expectancy for your compressed air system.
So, regulating your compressed air unit has three benefits.
- You will run your pneumatic tools well.
- You can streamline applications to increase the life expectancy of your unit.
- You will save on your energy use.
What You Should Do Before Adjusting Your Pressure Regulator.
Before you can make changes to your compressed air unit’s pressure regulator, ensure the settings are what they should be. It is always better to read the manual that came with your equipment and follow those instructions.
Air compressor designs and brands are different. The installation process will not be the same. Once you have everything set the way it should, you can do some adjusting with the regulator.
Use the steps below as a guide.
- Ensure your compressed air unit and application tool are compatible
Our first step is ensuring the specs of your air-powered tool match the specs of your compressed air unit. You need to know that information before connecting the two.
Mismatched specs can damage both the compressed air machine and the tool attached to it. Imagine plugging a 240-volt device in a 110-volt socket or vice versa.
Make sure that both pieces of equipment can work well together.
With that out of the way, you can begin setting up your compressor and learn how to use your system’s pressure regulator. - Connect your compressed air unit and turn it on
The first thing you have to do is connect your compressor to a power source and ensure it is on. The way to turn on your compressed air unit may differ with each model. Most times, you have to press a power switch. Do not turn on the power switch before plugging the compressor. - Let air into the tank
Once you have the compressor running, allow the tank to fill. The filling process should not take very long. A telling noise will let you know when the tank reaches capacity. It should only take a few minutes, and there is no need to stop the air on your own. Do not switch the unit off.
Remember that the PSI of your compressed air unit will determine how long it takes to reach capacity. So air compressors with tanks that have a PSI rating of 135 will take five or so minutes. The higher the PSI, the longer it will take for the tank to fill. - Connect the compressed air unit with your pneumatic tool
Take your air hose and connect one end to your air-powered too first. Connect the other end to the compressed air unit. Not the other way around. You will see the area where those connections need to be made on each piece of equipment. If you have difficulty finding the connection port, consult the manual to locate it.
How To Adjust Air Compressor Pressure Regulator
Now we answer the question of how to adjust air compressor pressure regulator.
Once the steps above are complete, it’s time to learning how to adjust pressure regulator on air compressor.
- Find The Knob/Lever
First, find the knob for the regulator. The regulator on many air compressors have knobs to the right side of them. But this can vary between models.
The knob may have a locking feature. To get it unlocked, you must pull the knob up. When you press the knob again, the locking feature will take effect again. - Raise The Pressure
It is a good idea to set your equipment’s pressure regulator a little bit higher than what your air tool needs. That’s because pressure drops can happen when the air leaves the tank and enters the piping or air hose. Raising the pressure by a small amount will make up for that loss.
If this feature is part of your compressor, pull the knob. Turn it to the right to increase the pressure. You will be able to tell that the pressure is rising. - Lowering The Pressure
You may also want to decrease your air supply.
Turn the knob/lever to the left to the left if you want to lower the pressure. Doing so will make the PSI drop. When you get the correct pressure, run your tool, lock the knob again. At this point, you are ready to use your air-powered tool.
Once you find the pressure your want, push the knob back to lock it.
If you experience a loss in pressure when using your air tool, you can make changes to the regulator again as you need.
Frequently Asked Questions
Here are some questions about pressure regulators that many compressed air ownwers want answered.
How Do I Read My Air Compressor’s Pressure Regulator?
Reading the results of pressure regulators is easy. All it takes is studying the display as the needle moves. It will change position, either rising or falling, based on how much pressure is in your tank.
Watch the needle so that you can match your air-powered tool’s PSI value with that of your compressed air unit. Remember, if they are too uneven, your equipment will fail.
Do Pressure Regulators Need Maintenance?
Like every other part of your equipment, you can perform maintenance checks on your compressed air unit’s pressure regulator.
The constant movement of operating pressure will cause damage to this piece of equipment over time. Your regulator can crack, which will lead to leaks. If your regulator has a crack or leaks, there is no fixing it. You must replace this device.
Consult the instruction manual that came with it to find out how regular those checks should be.
What Happens If The Valve On My Pressure Regulator Breaks Down?
You will notice a failing regulator valve in one of four ways.
If you have a crack in your regulator, air will leak out of it. You will see a drop in pressure.
Do not forget that as you use the pressurized air stored in the tank, the PSI drops. When it gets to the lowest level, the motor kicks in. The tank refills for a certain amount of time, giving you access to more compressed air.
With a cracked regulator, you will run out of air faster. This will put a strain on your compressed air unit because the process has to repeat itself more often.
The second thing you will notice is that you have no control over the pressure. That means you will lose the ability to raise or lower the air pressure to match your air-powered tools. Both your pneumatic tool and compressor can suffer damage as a result.
The third thing you will notice is a reduction in air flow. Once the pressure drops, this is bound to happen.
Here is the worst thing that can happen when a regulator valve malfunctions.
The valve will fail, and it will not allow the pressure in the tank to escape. The tank then gets too much pressure. Because of that, the motor will keep running. Remember, the tank should stop filling after a specific amount of time.
If you notice the motor of your compressed air unit runs without ever stopping, switch it off. Get the part replaced before turning it on again.
You can learn to do maintenance checks yourself. It’s a simple enough process. Or you can enlist the help of a professional to do so for you.
What Is The Difference Between Pressure Switches and Pressure Regulators?
The job of a pressure switch is to protect your compressor against too much and too little pressure. Both of these can damage regulator components, the compressed air unit, and your pneumatic tools.
The switch performs two functions. When the pressurized air inside the tank reaches its upper limit, the switch kicks in and turns the compressor pump off. That way, there is never too much air in the tank.
The opposite happens if there is too little pressurized air in the tank. Whenever the pressure drops to the minimum level, the switch kicks on again, starting the compressor so it generates new pressurized air.
Most compressed air units have a pressure switch preset to factory mode. There might be no need to activate or change it. The kick-in of the switch will be automatic once the pressure reaches the upper or lower limit the machine can have. But, you do have the option of making adjustments to when the switch responds. Your decision may be based on the application of the tool or because you want to save on energy consumption.
In short, pressure switches and regulators serve very different functions. The switch protects the compressor from too much pressurized air. It also refills the air whenever the pressure drops.
The regulator only controls the amount of air leaving your compressor to drive the pneumatic tool in use. It protects the pneumatic tools from damage.
Do I Need Multiple Pressure Regulators?
How many regulators you need depends on how many tools you run on your compressed air unit at the same time.
If you only use one tool, and that tool connects to one hose, you only need one regulator.
But if you perform several applications together, you will need a regulator to adjust the air driven into each tool. Or, you can use the same regulator, but you would have to readjust the regulator every time you change the instrument attached to it.
What Is The Correct Pressure For My Air Compressor?
Pneumatic tools differ by function and manufacturer. No two will be the same. As such, you can only set your pressurized air system to match the instrument you want to connect to it.
The specifications for each piece of equipment should be on their bodies. Or you can also consult the manuals to direct you. Remember that the specifications of both tools should match.
You should never disregard the recommendations made by the manufacturer of your equipment. It’s the only way to get a job well done and ensure the compressor and air tool suffer no damage.
Sometimes, it is safe to go over the recommended amount. But never do this by more than 20 percent.
The 20 percent is to make up for any pressure drops your compressor might experience. That way, your air-powered tool will not register any pressure changes and your finish will be perfect.
Conclusion – How To Adjust Air Compressor Pressure Regulator
Learning how to adjust pressure regulator for compressed air is a necessary skill.
Most modern compressed air machines come equipped with these devices. They are a vital component of your compressed air machine. That is why Learning how to adjust pressure regulator for compressed air is a necessary skill.
These regulators are there to ensure that your system does not deliver too much air to your pneumatic tools. They ensure that your application receives the right amount of pressure for seamless function and a perfect finish. At the same time, they also prevent you from wasting energy by using too much air, which will save you money.
But, regulators can only do that job well with proper maintenance. And learning how to adjust air compressor pressure regulator will also improve the way your tools function.