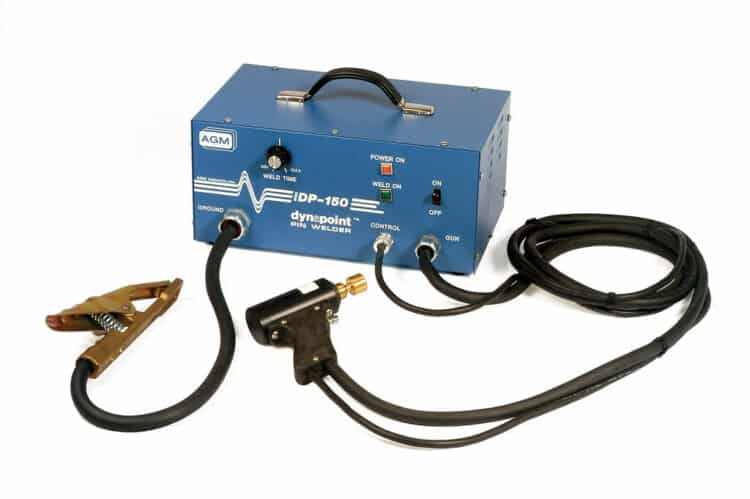
When it comes to welding, the dangers are inevitable. So ensuring that your safety comes first, you must provide your welding and doing everything right. One of the right things is to ensure that your welding machine is always grounded before you start. Bellow, we will give you a complete guideline on how to ground a welder and reasons why you should.
However is it possible to weld without grounding your welder? Yes you can. But there are risks involved that you can avoid. It includes:
- getting yourself electrocuted
- damaging your machine
- damaging your work.
All the above you can avoid by grounding your welder. If you still don’t know how to ground your welder or want to know more on why you should ground your welder. Read on.
Table of Contents
everything you need to know on how to ground a welder
Some welders come with an already installed grounding, therefore, providing necessary safety for you to work with. However, not all welders have this feature. It’s best to check first before making an assumption. You can check on the rating plate for a box within a bot symbol which means that yours is already grounded. If you are still not sure how to look, it is best to speak to an expert.
Additionally is you are operating a small welder that requires about 110v. It is most likely to already have been grounded. Always ensure that it is always plugged into the grounding outlet. Most importantly, do not remove the grounding plug on the plug. This is a dangerous move putting everyone in danger.
Types of grounding
Before you get to know, you must know the type of grounding that your machine uses. Below are the most common grounding techniques you may find.
- Grounding connectors
- Double insulation
- Grounding pins in plugs
- Test circuits
- Workpiece grounding
Many welding machines contain a flexible cord that is installed in the outlet. Few devices have a permanent wire and a grounding system. When you trace the wire back through the electrical system, you may be able to see the metal rod that connects your machine to the ground.
If you work with a welder, but it is not grounded. There will be no place for electricity to go to. Yes, there will be an arc but no weld. If your welding machine is not grounded and you’re not insulated, the electric current will go through you to reach the ground during arc welding
Many of the smaller machines utilize pins at the far end of the power or to conduct operations. When the machines are plugged in, the grounding conductor operation is automatic. On this machine, avoid the use of adapters because it will prevent the grounding by preventing the pin from connecting.
Test circuits are purchased to help you check on your grounding connector’s continuity. The 120 volts devise will indicate by light if the grounding is working at that particular outlet. They will show if you may require help to stabilize the grounding for your circuit.
A welding machine has circuits for welding through which currents are supposed to pass through. Terminus, cable, connection to the workpiece, gun, and workpiece are areas where welding current flows through. The welding circuit’s connection is not direct to the ground. Relatively it is isolated from it.
For this connection, you can use a metal table already grounded. Metal provides a suitable working area as long as you separate from the circuit connection. When you ground, your workpiece has the same benefits as other grounded equipment around. When there is any failure in installation in the welding machine, the voltage will be reduced between the workpiece and the ground.
You will use a spring clamp to connect your workpiece to the table for this type of connection.
- High frequency grounding
- Several machines for welding utilizes stabilizing and starting circuits that have high voltage frequency. As seen in the Gas Tungsten Arc Welding (GTAW), the components may reach frequencies that measure in the megahertz range.These frequencies may be so high that, at times, they may interfere with radio or television frequency. One way of reducing the release of high radiation signals is by grounding the welding circuits. There are instructions from the welder’s manual that instruct you on how to ground a welder to minimize radiation effects.
- Vehicle mounted and portable welding generator grounding.
- These vehicle-mounted or mounted welding machines are used for remote welding. They can supply from 120- 240 voltage power. In most of the areas they are used, there is no reliable grounding that you can apply.
Should the generator frame be grounded? When it comes to this question, you should consider the rules of grounding. It all depends on auxiliary, power generation, and specific design.
These are the requirements that are needed in order to ground the generator frame.
- Mounting of a generator must be on a trailer or track
- By the using plug arrangement and cord, where the power is taken
- The receptacles contain grounding pins
- The generator is connected to the trucks frame.
- Always consult with your local (NFPA) for guidance.
- Extension cord grounding
Extension cords get damaged over time while lying on the ground. That is why it is best to always ensure that you continuously test them. The receptacle circuit tester will help confirm if your extension cords are still in good working conditions.
How does electrical grounding work
When grounding your welder, all you need to do is clamp your ground clamp on your workpiece. The best metal to work with is clean and ensures that it is close enough to your piece. It should ensure that there is enough conductivity to prevent sparking and shocking you by grounding.
However, you should have a dumper if you need to avoid the current running through you. Some of the best dumpers are wood so ensure there are to your grasp.
Inside the grounding clamp, there is a strap that gets attached to the lug. There are contact plates that are on or even inside the clamp. While welding, this plate is likely to get burnt, and eventually, it will completely burn off. When this happens, there is no conduction of electricity by the clamp. Always ensure to check on them and do regular maintenance. Replace them when necessary.
Large clamps have great grip due to their large jaw teeth and giant spring. Also, they are made from a highly conductive metal. They are made with bolts that make contact in the cylinder for the cable you will be using instead of the usual nut hook and studs used for average cables.
To ensure that your ground won’t come loose and there won’t tugs on the cable tighten. And squeeze the contact pad so that tugs happens on the clamp if you have a working table made out of a conductor. You can ground it. This is done by clipping the ground on your table. Also, ensure to remove the ground out of the way so that you don’t trip.
It is important to remember that since your table is now ground, avoid leaning on it. Or you may get shocked. If it is a must for you to lean on your table, you can take the clip and clip it on your work. If your job is big for your clip, you can use a giant clip to clip it on your work. Then take the ground clip and clip it on the huge clip. Then your table will be safe to lean on.
If you’re working on a much smaller workpiece that even you can’t clamp. Then you can clamp it on your work table. When attached to the table, it means that your table is already grounded. So you have to avoid leaning on it. If you must lean, you should invest in the welding sleeve that protects you from sparks and spatters, UV radiation, heat, and even shock.
If you have some gloves in your workshop, you can lay them down to areas where you’re going to place your hands. Or you can use a dry piece of wood.
Where top put grounding clamp while welding
When welding, one important thing that you need to know is where to put your grounding clamp. It needs to be on the base metal that you’re welding. One other thing, it needs to be close to where you’re welding. You can place it under the plate you’re welding on. Just ensure not to clamp it on anything leaning on the will.
Metal workbenches or tables are always the descent areas to clamp your earth. Also, you need to ensure that the place that you’re attaching your clamp is clean and free from rust. If it is clean, it will interfere with your welding.
While grounding also ensures that where your clamping your ground will not interfere with your work. This is to ensure that you produce good clean welds and that you don’t get shocked while welding.
Is ground on a welder negative or positive?
This is usually confusing to many, especially first-time users of welding machines. But this is a huge mistake when confusing where the ground should go. When attaching your welding cable, you should attach the positive terminal to the one leading to the electrode while the negative one will lead to the work clamp.
To answer you, we have to know the polarity requirement for your weld. Your polarity requirement will either be positive and negative, and the other stud gets the ground. It is essential to know that while purchasing your equipment that your work does ground anything. You have to ground your machine yourself, to have a safe working environment.
The type of grounding that we are using in this article is neither positive nor negative. Grounding is achieved by attaching a separate wire or clamp leading to the cover of your machine. And therefore directly linking it to the ground.
Worktable should always be grounded. You can achieve this by using the building itself or connecting a cable to the table. This factor does not involve the positive or negative studs on your welding machine.
So this means that neither positive nor negative studs are to be used for grounding in welding safety. That is the reason why clamps are always used.
Why should I ground my welder
Below are reasons why grounding is important for every welder:
- Grounding prevents the build-up of voltage.
- Grounding prevents the welder from being electrocuted.
- When there is no grounding, there may be no current flow to the workpiece to assist with welding.
What happens if have bad ground while arc welding
When you have a bad ground, it is likely to have voltage loss, leaking of current, or even low current transmission. This will lead to poor welds, and you may end up adjusting your machine regularly with minimum results.
Due to the broken ground or poor grounding, it may lead to problem build-up. The area with the problem will heat up. And may lead to other issues, and the final result may lead to machine breakdown. For these reasons, you must ensure that there is proper grounding.
As shown, your ground must be functioning correctly. If your clamp is dysfunctional, ensure to purchase another. To ensure to keep producing quality welds and make sure that your machine doesn’t break down.
Final thoughts
When it comes to knowing how to ground a welder, you will have to consider many factors. This includes types of grounding, where to place your ground, how grounding will help you. Also, if you fail to ground your welder, you’re likely to get electrocuted.
Welding machines use a lot of electricity while welding, and ensuring that your appliance is grounded is essential. Electricity usually chooses the easiest and nonresistance path to go to the ground. If you’re working with a grounded machine, then you will be safe from shock.
Additionally, always check if your ground is working correctly by the use of test circuits. If your grounding cable has malfunctioned, ensure that it is replaced to avoid any further damage.