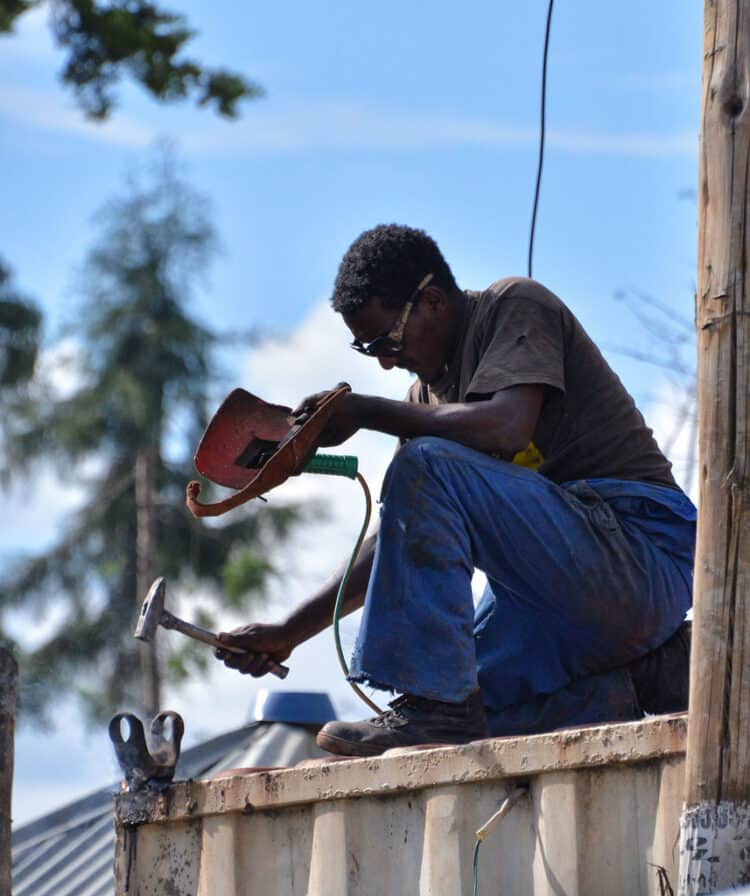
Whether you are a novice or an experienced welder, a weld with bends, buckles, and distortions is bad news. It can make your designs messy and un-proportional. The final product can make you lose clients, money and feel you have wasted your time. Welding distortion is inevitable even for experienced welders.
When you get a warped metal after long hours of welding, you feel frustrated. But is it the end of the road for you? If you are here looking for answers on how to straighten a metal sheet after welding distortion, you are on the right page.
In this comprehensive guide, we will look at what causes distortion in welding and the factors that influence this problem. We will also highlight how to control this distortion and the various metal straightening techniques.
Table of Contents
What is welding distortion?
As you heat a localized weld when joining two metal components, the high welding temperatures expand the metal. This expansion spreads until it reaches the cooler parts of the metal, which cut short the expansion. Contraction comes in due to the cooler conditions on the far ends of the joint.
This expansion and then contraction create residual stress that causes bends and buckles. If the thermal stress surpasses the weld’s yield strength, the metal changes its molecular properties and deforms. Welding distortion refers to the uneven and non-uniform appearance of the welds.
What causes welding distortion?
Distortion in welding occurs due to the following reasons:
- Internal stresses
- Heat cutting
Internal stresses
The internal stresses are natural forces in the metal components. External activities influence the level of these stresses. These activities include welding, heating, mechanical forces and chemical treatment
When these internal stresses are below the elastic limit of the metal, they have an insignificant effect on its structure. However, if the residual stress exceeds the elastic limit, the metal’s physical properties change. Change in physical properties causes distortion, which is visible to the naked eye.
Welding distortion results from two kinds of stresses. These are:
- Tensile stress
- Comprehensive stress
Tensile stress
This stress is an opposing force exerted by the cooler parts of the metal on the warmer area as it expands. This restriction forces the expanding metal to halt, causing warps and bends suddenly. In some cases, the metal may crack.
Comprehensive stress
When you heat a localized area on a piece of metal, the warm temperature travels along the length of the metal uniformly. As the metal expands along the longitudinal axis, the parent metal edges restrict the expanding material causing distortion.
Heat cutting
The distortions in your welded pieces may not result from welding after all. Some of the metal components come with distortion from the manufacturer. It is important to check your steel sheets and other metal pipes when obtaining them from your supplier.
But how do these distortions occur during manufacture?
At the manufacturing plant, machines cut long pieces of steel into sizeable plates using heat. The edges and joints are also shaped using thermal tools. The heat generates residue stress as the areas next to the cutting point start to expand.
When these adjacent parts contract, the metal’s final measurements are different from the original. This change causes a crooked look with bends. Since cutting is an automated process in most manufacturing plants, the steel plates are not straightened.
What are the different types of welding distortion?
Your welds will get distorted in these main ways:
- Longitudinal deformation
- Transverse deformation
- Angular distortion
- Bowing
- Buckling and warping
- Twisting
Longitudinal deformation
This distortion occurs when welding along the longitudinal axis of your metal sheets. The welding distributes the heat along the length of the metal, causing uniform expansion. When welding stops, the metal contracts uniformly, and the result is a shorter and deformed weld. Longitudinal shrinkage causes the metal sheet to bow.
The most vulnerable welding for longitudinal deformation is butt joint welds. The reason is that when you join two welds together along the axes, the heat applied on the inside contrasts with the temperature of the outside edges. Thus, the insides expand and contract more, thus creating a bow.
Transverse deformation
Unlike in longitudinal, where the expansion happens along the metal axis, transverse distortion results from the weld expanding and contracting across the axis. In this case, the widths pull towards each other, causing a change in dimensions.
This form of deformation results when the contraction force is more than the expansion. This process gives rise to a weld with a narrower dimension, which can alter the end product. The metal can even assume a different shape upon completion, which ruins your desired design.
Angular distortion
Some welding sequences form angles. These designs include butt, corner and lap joints. The metal expands and contracts along with the angles, making one of the pieces bend upwards. You end up having deformed T-joints with concave or convex bows along the length of the metal components.
Welds with V-joints are vulnerable to angular deformation when the transverse contraction is not uniform between the upper and lower metal sheets. This contrast in internal stresses causes the top weld to pull the bottom weld upwards, resulting in a cup-shaped bow.
Bowing
When you weld a metal plate or steel sheet along its perimeter, the heat does not reach the central parts of the piece of work, especially for thick welds. The edges expand and shrink as you apply the heat. When the temperature falls, the welds contract at the edges. This expansion and contraction cycle causes the edges to bend, but the centre of the weld remains unchanged. This distortion results in a bow-like or dish-like design.
Buckling and warping
This kind of distortion happens when the heating and cooling is complex. The different stresses cause a combination of longitudinal, transverse and angular deformations at a single joint. The different residual stress expanding and contracting in different directions gives rise to the non-uniform buckles.
A warp forms when a metal bends between several joints. These warps can be many in the length of the metal. A buckle is common along the width of the weld. Since contraction along the width reduces the dimension of the metal sheet, flattening it can sometimes cause cracks.
Twisting
This kind of distortion is common on butt joints, whereby the metal components expand and contract along the longitudinal axis. Still, the two sides of the neutral axis are not balanced. In this case, the residual stress on either side of the neutral axis is not equal. The tension created results in twists.
You can avoid this distortion by creating tack welds before the actual welding. You may also balance the residual stress on each side of the neutral axis. A mix-up of different stresses when a joint is vulnerable to longitudinal, transverse and angular distortion also causes twisting.
Factors influencing the formation of welding distortion
Welding distortions are not similar and do not occur randomly. There are factors that either increase the chances or work in favor of reducing these buckles. The type of distortion and chances of having one depends on:
- Welding components properties
- Thermal input
- Joint outline
- Welding technique
Welding components properties
The properties of the parent material influence the likelihood of getting a distortion. One of the properties is the co-efficient of thermal expansion, a measure of how a material change in size in relation to change in temperature. In distortion, the higher the coefficient of thermal expansion of a material, the easier it is to bend or distort.
Pure metal and an alloy will also have varying level of distortion. Therefore, understanding the properties of the metals you are about to weld is vital because it will inform you of points to consider and precautions to carry out.
Another physical property of the weld is its thickness. A thin metal conducts heat faster, thus expands and contracts faster. Also, when welding metals of different thickness, the thicker one is likely to pull the thinner piece towards its direction, thus causing distortion.
Thermal input
The higher the heat input, the higher the chances of welding distortion. More heat melts more metal material, thus requiring more filler and electrodes. Using more of these materials prolongs your welding period, which could lead to over-welding. Over welding consequently raises the chances of getting a buckle or a bowl as the weld contracts back to its original shape.
Another factor here thermal input plays a role is the number of passes required before completing a weld. Short multiple passes increase the chances of distortion. You should go long single passes to reduce the expansion and contraction cycles, thus reducing welding distortion.
Joint outline
The type of joint and the amount of metal or welding beads placed at the joint influences welding distortion. Butt and fillet joints are more vulnerable to deformations due to the difference in stress between the co-joining plates. Utilize the right amount of fillet and prepare the joints beforehand to reduce buckles, warps and twists.
Preparing in advance before you start welding makes the actual welding an easy affair. This preparation includes strategically placing the welding components together according to the joint, be it corner, butt, lap or tee joint.
Welding Technique
The welding pattern and the amount of weld used determines the likelihood of distortion. Generally, manual welding has interrupted heat input, and the expansion-contraction cycle is likely to cause distortion. On the other hand, automatic and semi-automatic welding produces a uniform thermal input until the welds are complete.
Manual arc welding also creates unnecessary movements in the course of welding. These interrupted heat inputs cause non-uniform expansion and contraction, resulting in bumps, bowls and warps between the joints.
How to reduce or control welding distortion
We all want a clean and seamless weld t the end of the welding process. But that is only possible in a perfect world. Well, in this world, no matter how good or experienced you are, you always miss some points and end up with a distorted weld.
However, you can reduce or control the level of distortion. These activities fall under three categories:
- Activities to do before welding
- Activities to do during welding
- Activities to do after welding
Activities to do before welding
This phase involves preparation activities that lay a good foundation for the actual welding. These procedures are:
Design the joints well
When you prepare and design your joints well, you are likely to use minimal welding volumes. The welding process will also be seamless and take a shorter time. By avoiding over-welding, you finish your welds with less distortion.
This procedure is vital, especially if you have butt, corner and tee-joints on your piece of work.
Preheat the metal components
When you preheat the parent materials before welding, the metals get accustomed to the temperature. The drastic temperature change when you apply heat without preheating is the primary cause of distortion. The instant expansion and contraction makes rigid buckles and may sometimes crack the metal.
Preheating the welds reduces the temperature deviation. The stress level depends on the temperature difference, the lesser the variation, the less likelihood of welding distortion. In addition, preheating introduces some familiarity to the stress in readiness for the actual weld.
Heating your welds beforehand also cuts the amount of initial heat required to penetrate the targeted joint. This technique comes in handy when dealing with thick parent materials. Less initial heat means the stress will be little, and that reduces the chances of deformation.
To preheat your welds, heat the targeted areas lightly and slowly. As you gently heat the localized areas, the heat spreads across the length of the weld. After the metal becomes accustomed to the heat, it will be unlikely for the melt to experience excess stress that causes buckles.
Preset your materials
Before you can start welding, you need to assemble your welding components in a way that would reduce the likelihood of distortion. These include wedges, levers, and the two metal components.
Use a jig or clamp to hold your work in place
Whenever you are welding, hold your parent materials together to minimize movement. Use a jig, clamp or fixture to hold the upper and lower welds in place. This technique improves accuracy since the sequence will be intact as you weld.
These tools may not remove the distortion possibility entirely, but the reduced motion maintains efficiency and precision. The less the movement, the more consistent is the heat application, thus reducing buckles.
You may go the extra mile to introduce a water-cooled jig. This tool reduces distortion by removing the heat from the welding components as you weld. Likewise, you may create strong-backs to control the movement of the two weld components.
Create tack welds
Just like jigs and clamps, tack welds hold the pieces to be weld together to minimize movement. The only difference is that you have to create them using the torch and filler material. They are temporary but keep the two-parent pieces together until you make the final weld.
Tack welds are more suitable for thin welds because it will be easier to remove the tacks once you finish the welding.
Techniques to do during welding
In the course of welding, these techniques will help you prevent or reduce welding distortion:
Make a good welding pattern
When doing a couple of welds, planning your welding sequences in the right way is vital. The pattern should distribute heat uniformly and make the pieces of work rigid. With a regular heating and cooling cycle, the residual stress normalizes and cannot outdo the yield strength. This steady expansion and contraction reduce distortion.
Level up your welds
In this technique, you need to ensure the residual stress on each side of your joints is equal. A balanced weld is one with joints close to the neutral axis. The neutral axis is the place on your metal plates with no natural longitudinal or tensile stress.
Therefore, when your joints are close to the neutral axis, there will be minimal stresses when welding. The less the stress, the less the distortion. The balanced expansion and contraction are crucial when welding round parts, corner, fillet, and butt joints.
Make few long passes
Use few long passes with heavier electrodes instead of many short passes with a small electrode. This technique reduces the accumulation of residual stress. Short passes produce more stress at the end of the welding process. Therefore, if you are working on several joints, make long passes and use a bigger and heavier electrode to reduce the distortion.
Adopt the back step welding technique
Back step welding reduces the effects of heat application, whereby you regulate expansion and contraction. This technique is effective against transverse distortion, such as in tee and butt joints.
Suppose you are welding your plate from left to right. Back step welding creates the co-joining beads from right to left, which is in the opposite direction of the weld.
If you weld continuously in the same direction, both the weld and bead formation direction happens in the left to the right direction. This method causes cumulative transverse stress that reduces the dimensions of the parent materials.
However, back step welding creates a restraint on the edges of each plate. As you proceed in the left to the right direction, the expansion and contraction along the edges of the welds pull them together. Continuous back stepping reduces the transverse stress, consequently reducing distortion.
Reduce welding time
As opposed to what most welders think, a thick welding bead does not indicate strong welding. Instead, the thick layer increases the time utilized joining two metal plates. Using too much filler material and heavy electrodes can lead to over-welding.
The more you weld a piece of work, the more the residual stress buildup. The extra residual stress caused by the cumulative expansion and contraction causes distortion. In light of that, minimize the time spent on the weld by using a light electrode and working fast enough.
Weld intermittently
Continuous welding can exert a lot of heat on a joint. The cumulative heat causes the over-expansion of metal and creates residual stress that surpasses the elastic limit of metal. The excess heat and more residual stress cause changes in the molecular structure of the welded joint. Upon cooling, the damage is already done, resulting in distortion.
For this reason, take breaks between the welds to give the metal some time to cool and contract to the original formation. Intermittent welding controls the amount of reinforcement applied to a joint, thus regulating the thermal stress.
Weld different joints alternately
When working on a project with several joints, alternate the heat application from one side to another. The alternation gives you a window to notice bending parts and correct them sooner before the distortion gets out of hand.
Activities to do after welding to control the distortion
Peening
So you have done everything in your power, but you still get few distortions, don’t beat yourself up. You can use the blunt part of a hammer to straighten the metal plate. This process is called peening, and the part you are hitting with the hammer is the weld bead to relieve stress.
Picture this process as pulling some threads after stitching when you realize the seam is too tight to lay flat. Similarly, peening allows the metal plate to relax and assume its original or the desired appearance.
Controlled heating
This method is similar to peening in that it relieves the buildup stress after welding. Instead of using mechanical force, you use steered heat on the distorted part. Although this method is not common, a situation could be unfit for mechanical stress relieving, thus calling for heat use.
Thermal stress relieving corrects the buckle or bow by expanding the localized distortion and then using adjacent cooler parts as restrictions to prevent further expansion. The cooler parts also initiate contraction, thus forcing the bend to straighten. This step utilizes a heating torch.
Straightening steel after welding distortion
Welding distortion in steel is a nightmare to many welders, both novices and veterans. If you spot a slight bow, warp or buckle on your welds, take heart and follow these corrective techniques on how to straighten bent sheet metal:
- Mechanical corrective techniques
- Heat corrective techniques
Mechanical corrective techniques
The first method on how to straighten is using mechanical metal straightening tools such as hammers and presses. In this technique, you apply force with the mechanical tool to level a bump, concave or convex bow.
Hammering
Use a hammer or a similar tool to exert force on the bent steel part until the metal flattens. One downside of hammering is that it requires mechanical force, thus exhausting. In addition, applying too much force can cause fractures and cracks on the welds.
Tools coupled with a hammer during this process include a wedge and a pneumatic ram.
Hydraulic press
This technique has fewer risks than hammering because you press the joints using controlled force. Welds with bows and angular distortion on butt and tee joints are the best fit for presses.
To use a hydraulic press to straighten a weld, place packing pieces between the metal piece and the press. Force the press down the bends using enough but not excessive pressure.
Mechanical corrective technique tips and tricks
For efficient mechanical straightening of welding distortion, do the following:
- When using a machine press, ensure no pets or other people are around as flying packing pieces could hurt them
- Fasten the packing pieces to the press’s platens
- When hammering, support the welds on the lower side to avoid reverse buckling
Heat corrective techniques
The use of heat in straightening re-introduces localized stress to soften and expand the metal. When the re-heated metal part cools, it contracts and returns to the original shape, thus correcting the distortion.
However, unlike in welding, where the heat exceeds the metal’s elastic limit, flame straightening heat should be below that limit to avoid inducing molecular changes to the metal. It would be best to restrict the heat to avoid over-expansion, which may worsen the distortion.
How hot does metal need to be to bend? Well, it depends on the type of metal, if it’s pure or an alloy. As a rule of thumb, steel and aluminium require less heat to bend than other high-strength metals such as tungsten.
Different metals need varying straightening temperature. Always consider the thickness and strength of the metal to decide on the amount of heat to apply. You can also let the behavior of the metal guide you on when to add more heat or stop the heating.
Are you wondering if all metals can be heat straightened to remove welding distortions? Aluminium, steel, copper, nickel and brass are suitable candidates when using localized heat application to flatten buckles and warps.
The following are the different thermal steel straightening techniques:
- Spot heating
- Line heating
- Wedge-pattern heating
- Oval heating
Spot heating
This technique is suitable for thin metal sheets with shallow bows and warps. You use an oxyacetylene torch to apply localized heat in the form of spots on the convex side of the bend. As the metal expands and cools, the warps flatten.
The best way to work the metal is by applying small heat spots until you correct the entire distortion. Large spots may cause more warps instead of flattening them.
Line heating
Line heating is mostly used to flatten angular distortion. You use the flaming torch to apply localized heat along a straight line. For instance, you can straighten a bend on a fillet weld by heating along the line opposite the welding bead, where the parent metals intersect.
As you apply the heat on the other side of the welding bead, the heat variation imposes residue stress that expands the metal. As it cools and contracts, the distortion flattens. Depending on the welds’ distortion and thickness, you may need to make more than one heated line.
Wedge–like heating
This technique is suitable for welds with complex sequences and thick metal components. When such welds bend, corrective measures use more heat and line heating intersecting to form a wedge shape. Wedge shapes ensure the heat spreads uniformly.
The process is suitable for correcting distortions such as edge buckling, corner warps and distortions involving two planes.
When you apply the heat evenly, the complex distortion expands then shrinks enough to create a flat plate. One consideration to make is to sketch where your wedge will pass through to balance the stress on either side of the neutral axis.
Wedge-shaped heating may require the use of two torches, one for either side of the neutral axis. The coordinated heating ensures the expansion and contraction cycle is simultaneous, consequently equating the pull. Different stresses could cause more buckling instead of flattening the distortions.
Considerations made when performing wedge-like heating to correct distortion
- The length of the wedge should be two-thirds of the width of the weld metal</li
- The width of the wedge should be a sixth of the length of the metal plate
Oval heating
Are you wondering how to straighten bent aluminium tubing? The oval heating technique will be your best bet. In this process, you use an oxyacetylene flame to apply localized heat in an oval shape. You create the localized pattern such that the longer side of the oval is along the length of the welds.
This method works the same way wedge-shaped heating does by distributing the stress simultaneously on either side of the neutral axis. The heated area of the pipe expands but the colder adjacent parts restricts the further expansion. The metal part contracts, flattening the bend.
Downsides of using heat straightening techniques
Using heat to correct distortions requires a lot of precision. If you apply too much heat, it could change the welds’ molecular structure, causing more buckles and warps. You end up with different bends instead of a flattened plate.
Conclusion
Welding distortion is inevitable, yet it frustrates you because you get undesired results and have to use more time to correct the bends. However, you can reduce these metal warps by applying certain techniques such as back step welding and using fewer passes.
But if you still get slight warps after welding, you can correct them by using mechanical and heat straightening techniques. Each of these techniques is suitable for different distortions. Understanding how the various straightening techniques work can inform you on the most suitable remedy for your distortion.