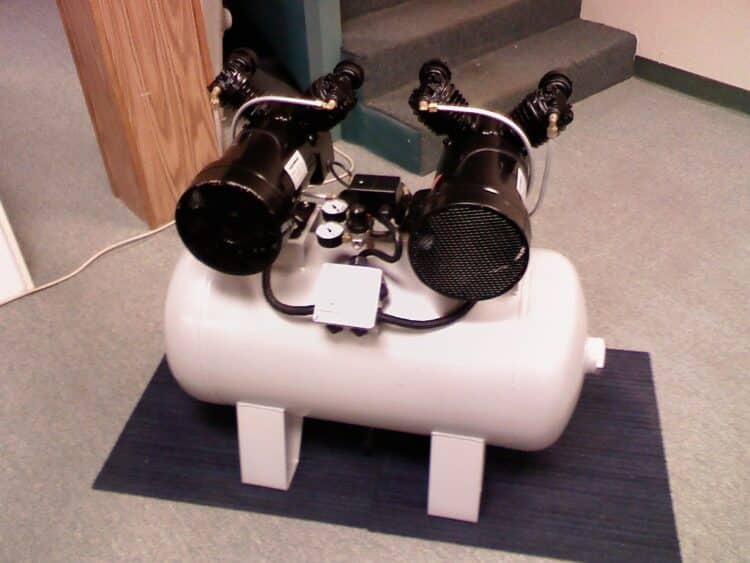
If you own an air compressor, then you should know how to maintain it. If you are a serious hobbyist and need it for your many creative ventures, then you should learn its many ways of proper maintenance. Knowing how to take care of it can save you money in the future and prevent any wasted time.
You have to be ingenious about this and create a compressor inspection checklist. This way, your air supply device would always operate to its full capability and not get damaged.
But first, you have to focus on one key question: how often should air compressors be inspected?
Table of Contents
Pump Oil Maintenance Checklist
If your device needs oil in the system, do not let it run without one in the system or a lube of low quality. The lubricant makers would not be held accountable for providing a substandard lubricating substance.
- You have to make sure the device is shut down unplugged from the electrical socket.
- You have to be sure that the device is placed on level ground, without anything bulky obstructing the surface.
- Remove the plug from the crankcase.
- Check if the oil inside the crankshaft and see if there is grime.
- The oil must not be too much and not be over the midway portion of the sight glass.
Pump Oil Substitution Checklist
Check first if the pump head and the other components along the device are hot to the touch.
- Before starting everything, be sure the device is shut down and unplugged from the power socket.
- Make sure the device is on flat flooring, with nothing obstructing it.
- Take out the fill cap.
- Put a small bucket below the oil drain slit.
- Unscrew the oil drain plug and let the oil pour out.
- After draining all the oily refuse, screw in the drain plug securely with the plumber’s tape to make the seal as tight as possible to avoid leakage.
- Pour in a high-quality compressor oil and do not go over the midway portion.
Air Filter Element Checklist
- Before starting everything, be sure that the device is turned off and unplugged from the electrical socket.
- Wait for a few minutes for the device to cool down.
- Unscrew counter-clockwise the filter cap from its base.
- Take out the filter element from the base.
- Remove the filth from the element by blowing or gently pounding it.
- Check if the filter element needs replacing. If it does, then do so.
- Screw back the filter cap tightly on the base.
Overall Compressor Maintenance Checklist
This part holds the answer to the question: “How often should air compressors be inspected?” Just adhere to these simple steps, and your device will have a long shelf life and would scarcely malfunction.
Before executing any maintenance checks, let out all the remaining pressure in the system, disconnect it from the wire socket or any other receptacle it connects to.
Daily Checklist
- Look for any leaks like oil or water appearing on the tank or the valves and fittings.
- Take a look at the oil level, b sure it is not over the half-way portion.
- Uncork the tank cap and let the accumulated condensation liquid drain out (no need if there is an automatic draining mechanism attached).
- Unscrew the main drain valve manually to let out the condensate. Be sure to collect it in a container so as not to make a mess.
- Intently listen if strange sounds are emanating from the device.
- Check if the covers and belt-guards are tightened securely in their proper place.
- Check on the engine is fueled properly (if gas-powered) and oiled as recommended by the compressor’s fabricator.
- Take a look near the device if it does not have any tools, rags, rubble, explosive or flammable materials scattered around.
- With compressors that are pressure-lubricated, look at the oil pressure in the system after turning it off, while it is still hot to the touch.
Weekly Checklist
- Pay close attention to the relief valves as the device is still functioning. If you notice it is malfunctioning, replace it immediately.
- Check on the air filter components, and clean it if it is soiled.
Monthly Checklist
- Examine closely if there are any leaks of air. Pour soapy water on the joints while it is still running, and look for any bubbling action.
- While the device is turned off and already cool to the touch, check if the screws, valves, bolts, and any other attachments are tightly screwed on. If some are loose, then tighten it up.
- Examine if the drive belts are loose or tight. Turn it tightly if necessary.
- If the external surface of the device is dirty, clean it using a damp rag.
Checklist, After 3 Months and/or 500 Operating Hours
- At this time, the petroleum lubricant may dry up. So after turning off the device and still warm, replace it.
- The compressor oil needs to be drained into a container.
- The oil sight glass needs to be cleaned.
Checklist, After 6 Months and/or 100 Operating Hours
- Once the device is off, check on the oil filter and replace it if necessary.
- If needed, also change the lubricant (only applicable to pressure-oiled models).
Checklist, After 12 Months and/or 2000 Operating Hours
- Set up a compressor maintenance package.
- After turning the device off and is still warm, replace the synthetic lubricant.
How a Compressor Inspection Can Benefit
With a little organizational talent, you can devise a way to collect the needed information and track the many changes that can happen. All the data will urge you to make the necessary changes and execute preventable measures to make your device operate in top condition. Here some other benefits:
- Can boost productivity.
- Can optimize efficiency.
- Can cut-down waste.
- You can plan for the future for your device.
- Can detect what parts needed to be fixed or replaced.
A Summary on How Often Should Air Compressors Be Inspected
The most important thing you need to remember is to take notes so that you can track your collected data. This way, you can budget for incoming expenses like repair and parts replacement. The essential data to take note of are as follows:
- Operating temperature
- Pressure levels
- Airflow