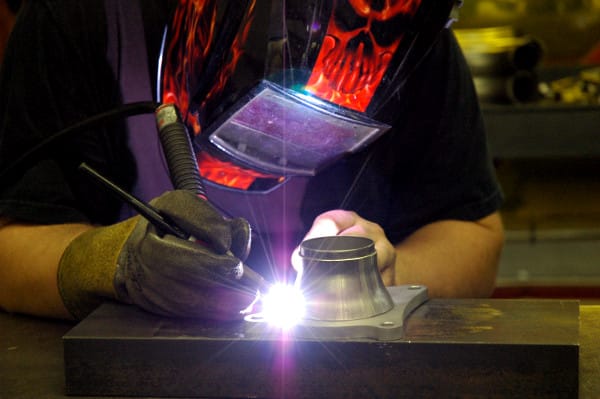
Welding is the process of fusing two or more materials–usually metals or thermoplastics– utilizing heat or pressure or both. This effectively forms a joint upon cooling.
The different welding processes are classified based on the type of pressure, heat, and equipment used to complete fusion.
TIG Welding is a popular welding process that demands skill to produce high-quality welds.
Table of Contents
What is TIG Welding?
The full name for TIG welding is Tungsten Inert Gas welding. It is an arc welding method that uses tungsten as the conductor.
A non-consumable tungsten electrode effectively transfers the current to the welding arc which meets the base metal. This forms a weld pool.
The filler metal is then fed into the weld pool by hand. At the same time, inert gases will prevent oxidation of the weld pool and tungsten.
The process produces a weld that is excellent in quality and clean in appearance. The resulting welds also share the same corrosion properties as the base metal.
What are the Best Materials to Use for TIG Welding?
TIG Welding is an extremely versatile welding method. It can be used on almost any metal and unique alloys.
It is most suitable for: aluminum, stainless steel, and nickel alloys.
TIG Welding is commonly used for thin sheets of metal, which require precise and intricate detail. A mechanized wire feeder will make the process more cost-effective.
TIG welding may not be a cost-effective option for thicker metal.
How does TIG Welding Work?
With practice and training, TIG welders can create high-quality and precise welds.
With one hand, a welder uses an electric torch to melt the base metal and create a weld pool, while the other hand is used to feed the filler metal into the weld pool. A thumb control switch or an accelerator pedal makes it easy to control and modify heat.
The Parts of a TIG Welding Machine
1. DC or AC Power Source?
TIG welding can be used with either direct current (DC) or alternating current (AC)–to provide the electrode with a steady and consistent supply of electrical currents.
In a DC power source, arc heat is distributed unequally with the cathode (positive) at a third and anode (negative) at two-thirds. To prevent overheating and melting, this produces an electrode that is constantly at a negative polarity.
Generally, steel or iron is welded with a DC power source.
AC power source is best used for aluminum. AC allows switching from electron negative to electron positive by default. This will allow electrons to penetrate the oxide layer of aluminum, effectively creating a weld pool.
2. The Work Lead
The Work Lead features a ground cable with a clamp. This is attached to the metal surface that will be worked on. Another cable on the work lead carries the inert gas, typically argon.
Inert gases help to protect the weld from contamination from the air.
3. The TIG Torch
The interior of the TIG torch features a small tungsten rod that is highly resilient to heat damage.
The tungsten rod can also be easily customized to work with a variety of materials and detail. Pure tungsten is typically used for materials such as aluminum and magnesium with an AC power source.
It is critical to choose the correct electrode diameter and tip angle for the chosen welding current.
For DC welding, additives such as: thoria, lanthanum oxide, and cerium oxide improve the welding arc’s performance. Thoriated tungsten works are used for: carbon and stainless steel, nickel, chromium alloys, and most ferrous metals.
AC welding operates at a much higher temperature. Generally, zirconia is added to prevent the erosion of electrodes.
A copper collet is used to adjust the length of the tungsten rod, which may be extended past the ceramic cup. The ceramic cup can also be easily replaced and customized based on the project requirements.
The copper collet features holes that will allow gas to move into the cup and around the tungsten.
Oxygen is excluded as it will contaminate the weld.
4. Starting-up the Welding Arc
The welding arc is started by forming a short-circuit.
To prevent electrodes from sticking to the surface, the Lift Arc technique may be employed to form the short circuit at a very low current level.
One of the most commonly used methods to start the welding arc is to use High Frequency or HF. The HF is achieved by producing several thousand volts in a span of a few microseconds to produce high voltage sparks, which will cause the gap between the electrode and material to ionize.
Once an electron cloud exists, the current can flow freely.
HF also works to stabilize the AC arc. While electrode polarity is reversed fifty times per second, the welding arc voltage is also extinguished.
HF sparks work to reignite the welding arc voltage at every reversal of polarity.
5. Control Switch
Remote control switches can be found either as a foot accelerator pedal or a thumb switch.
These control switches will allow the welder to seamlessly adjust amperage levels. It is important to keep a gradual and steady change in temperature as quick changes will damage your material.
TIG machines also allow the adjustment of balance, which is critical for welding aluminum. The balance will determine how deep the weld should penetrate the metal.
TIG machines also feature a choice between a normal and a pulsed mode. The pulsed mode will adjust the TIG welder amperage automatically, efficiently keeping down excess heat to create a more precise weld.
Inert gas
The type of inert shielding gas to be used will depend on the type of material being welded.
Argon is one of the most common shielding gases used for TIG welding.
The gas is versatile enough to work with a variety of materials such as aluminum, titanium, steel, and stainless steel.
Argon with an addition of two to five percent hydrogen will create cleaner welds due to reduced oxygen levels that will prevent surface oxidation. This will also produce a hotter welding arc, which will allow for faster welding.
On the other hand, argon mixed with hydrogen can cause hydrogen cracking in carbon steel. It may also promote metal porosity in aluminum alloys.
A combination of helium and argon increases the temperature of the welding arc. This will allow for faster welding speeds and a deeper weld.
On the other hand, helium and argon are costly, and it is difficult to short-circuit.
How to Start TIG Welding Process?
The manual process of TIG welding demands a high level of skill, which requires dexterity and precision.
While it requires more skill and is more time-consuming than other welding methods, the resultant weld is unparalleled in quality and appearance.
To get started on TIG welding, follow these steps:
1. Choose Electrode
Make sure that the electrode you are using is appropriate for the material you will be welding. A pure tungsten rod is used for aluminum, while other additives may need to be added for other base materials.
2. Prep the Electrode
Before you begin welding, the tungsten rod should first be shaped according to the welding project. You may grind the tip to a fine point for thin metals and to achieve intricate detail.
After preparing your electrode, unscrew the ceramic cup, then place the tungsten rod inside. Remember to screw the ceramic cup securely.
3. Select the Appropriate Settings
Select the appropriate settings for the power source.
* AC: Used for Aluminum
* DCEP: “DC, Electrode Positive”:For stick welding and balling the tungsten tip.
* DCEN: “DC, Electrode Negative”: For welding steel.
The “Cleaning/Penetrating” settings should also be adjusted. It should be enough to penetrate the base metal. Other settings to adjust include “Air on” and “Max Amps.”
4. Choose the Shielding Gas
Argon is one of the most versatile inert gases to use
For aluminum, use pure argon as the inert shielding gas.
For welding other metals, use a mixture of argon and hydrogen or argon and helium.
5. Gear Up
Before you start welding, make sure that you put on appropriate protective gear!
Spending a lot of hours at the welding table can affect concentration and cause eye strain from exposure to UV radiation and welding fumes. Rashes and burns may also be sustained without proper protective gear.
The essential safety equipment include:
* Welding helmet
* Closed shoes
* Leather welding gloves
* Welding coat
* Flashlight
* Stationary exhaust device
6. Prepare the Welding Area and Equipment
It would be best for your safety to have a large metallic table set-up in your work area. The metal surface will allow electric currents to flow through the metal efficiently. Clamp down your metals.
Spray your table with an anti-spatter to make clean-up easier. Remember to clean the surface of your base metal with a wire brush–this would ensure a clean and smooth weld.
Do a final check before you start welding. Using your dominant hand, start-up the electrode, and make sure that it moves freely.
7. Wield your TIG Weld
To prevent your metal from melting, start with the electrode about an inch away from the base metal. Next, adjust the amperage to heat up the metal. This will start forming the weld pool.
Start adjusting the heat of the torch.
Make sure that the weld pool is evenly heated by alternating sides–this will prevent your metal from warping. You can then start feeding the filler metal to the weld pool.
For aluminum, keep the rod to the electron’s side while feeding–a process called “leading” the electrode.
For steel, allow the electrode to travel down the weld line–known as “following” the heat.
What are the Advantages and Disadvantages of TIG Welding?
Advantages
Controllability
TIG welding produces high-quality welds because of the amount of controllability the process allows.
With the use of a remote control switch, heat and amperage can be controlled with considerable precision.
Detailed and Intricate Design
With the use of a thin TIG torch, a skilled welder with excellent dexterity can produce extremely detailed designs and curves. The TIG torch requires low amperage, which is ideal for working on metal and thin material.
Clean finish
The process requires only the addition of the necessary amount of filler metal. In this way, sparks and spatter are not produced.
Versatility
TIG welding is suitable for almost any metal and alloys. The remote control switch and the TIG torch make it convenient and easy for a welder to switch between working materials with varying thickness and quality.
Disadvantages
For TIG welding to be done effectively, a high skill-level requires focus, patience, dexterity, and hand-eye coordination. With proper training and practice, welders can learn the process and art of TIG welding.
What are the Applications of TIG Welding?
TIG welding is typically used when a project requires high-quality, precision, and cosmetic welding. Since TIG welding provides significant accuracy, this process works best on thin and small metals.
TIG welding can be used with a variety of filler metal and alloy options, making it one of the most versatile welding processes.
This versatility allows TIG welding to be completed with the most well-matched materials, making the weld extremely strong and high-quality. This makes it the perfect option for critical projects such as those in the aerospace and nuclear and power industries.
The combination of TIG welding versatility with metal and unique alloys coupled with precise and controlled application makes this welding process useful in a variety of industries, including:
* Energy
* Electronics
* Automotives
* Mechanized systems
* Aerospace and avionics
* Industrial sector
* Defense and Military
* Medicine
* Maintenance and repair work
Is TIG Welding a Good Career?
TIG welding machines require a high level of skill, requiring patience, dexterity, and precision. Training to hone your TIG welding skills will definitely be challenging, but it will open some lucrative career opportunities.
Skilled TIG welders may find promising career opportunities in industries such as aerospace, construction, electronics, and petroleum.