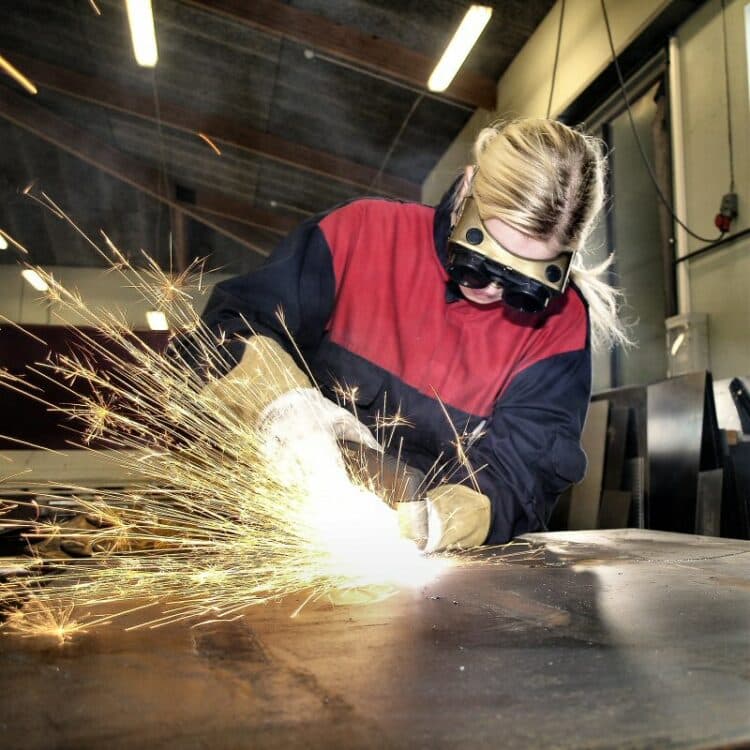
From welding in forges to modern welding, humans have been welding metal together for a long time and since then, we have been able to develop a lot of techniques. Each one has its own set of pros and cons.
This article will discuss the different kinds of welding and other useful information about it.
Table of Contents
What is welding?
Welding is a fabrication process that melts and fuses metals together under high temperatures. However, a weld can also happen when extreme pressure is used to fuse metals together.
Through welding, metallic structures are not just bonded together; they literally become one. Welding often uses a sort of shield to protect the components involved from oxidization.
What are the dangerous consequences of welding?
Before you start welding, there are necessary safety precautions that you must take. You have to be aware of the hazards and risks that can come from welding so that you can stay safe.
Electric shock
Live electrical circuits are what create pools of molten metal during an arc welding process. This is one of the most serious hazards faced by welders and is cause for serious harm and injury.
Noise damage
While welding, it is expected that you will be exposed to very loud noises for a long period of time. The measurement for loud noises is 85dB (A) and above but welding noises can go higher than 100 dB(A). This can result to permanent hearing loss.
UV and IR radiation exposure
Light is produced during welding. Not wearing the right protective gear or welding curtains can lead to painful conditions such as arc-eye. Long-term exposure to these flashes can cause permanent vision loss and cataracts.
Exposure to fumes and gases
Gaseous fumes are always present when welding. These fumes can easily enter your lungs and cause severe damage. Examples include but are not limited to pneumonia, cancer, metal fume fever, occupational asthma, and irritation of the respiratory system.
Burns
Due to the UV rays and presence of molten metals, burns are common in welding. Sometimes, minor burns and scrapes are unavoidable but severe burns are what happen when one skips the necessary safety precautions.
What are the safety precautions in welding?
In order to protect yourself, there are strict measures you have to take in order to stay safe while welding.
Wear the appropriate Personal Protective Equipment (PPE)
PPE protects you from long-term illnesses brought on by welding. Make sure they are of high quality and that there are no repairs needed. Standard PPE includes, but is not limited to:
- Welding helmets that have side-shields
- Respirators
- Ear protection
- Boots and gloves
- Fire-resistant clothing
Get proper training
Even taking an online course in welding can already give you so much information about the dos and don’ts.
Ensure your workspace is up to standard
Proper ventilation
A lot of gases are released during welding, and you have to make sure you do not inhale these gases.
No flammable materials
Sparks are created during the welding process, and you have to make sure they don’t catch anything flammable. Keep all flammable materials in a separate room, and make sure the structure you’re welding in is not flammable as well.
What are the different types of welding gloves?
Welding gloves are essential when you are welding. They protect hands from serious burns and that’s why you have to choose welding gloves that are of the best quality. There are different types of welding gloves for different types of welding. You also want to consider how much how well you need to move your hands while welding.
Different welding techniques generate different kinds of sparks. For example, MIG welding creates a lot of sparks which you have to shield yourself from, then clean up afterwards.
Gloves are also created with the use of various materials. Leather is preferred by most users because they don’t conduct electricity, they’re durable, and they don’t absorb heat. There are also different types of leather from different kinds of animals:
Pigskin
Leather made from the skin of a big works great in work environments that are wet and oily because the material is tough. It is recommended for stick welding, TIG welding, and MIG welding.
Horsehide
Leather made from the hide of a horse is recommended for use in TIG welding because it is comfortable and durable at the same time.
Cowhide
Leather made from the hide of a cow is actually very common. Like horsehide gloves, they are both comfortable and durable. It is recommended for MIG welding and stick welding.
Goatskin
Gloves made out of goatskin have the best tensile strength and unparalleled abrasion. At the same time, they feel supple and soft. These gloves are recommended for TIG welding because they offer the most dexterity.
Elkskin
Leather made from the skin of an elk is recommended for MIG welding because it gives off a lot of heat. It also has a longer hardening time, unlike cowhide gloves.
Deerskin
Since deerskin gloves are also dexterous, they are recommended for TIG welding since they are so soft and flexible.
What are the different kinds of welding?
Arc Welding
Arc welding techniques often use a filler material. It is usually used to join metals such as stainless steel, nickel and copper alloys, aluminum, and cobalt and titanium. Its processes can vary depending on which industry is using it. For example, power industry would have a different process to arc welding compared to the aerospace industry.
Metal Inert Gas (MIG) Welding
MIG welding produces heat through the formation of an arc between a consumable metal electrode and the workpiece. A weld bead is formed by the melting of the electrode. This metal electrode is actually a wire that is small in diameter that is fed from a wire feeding spool gun through the contact tip. At the same time, the welding torch feeds a shielding gas.
Has bottles are often used for the shielding gas and compatible filler materials. Aluminum wires have to be used while welding aluminum, steel filler wires have to be used to weld steel, and so on.
Tungsten Inert Gas (TIG) Welding
TIG welding is not recommended for beginners because it is more difficult compared to other welding techniques. The other term used to refer to TIG welding is Heliarc welding. In this type of welding, two hands are used. One holds a TIG torch while the other feeds the rod.
The TIG torch creates heat and arc. These are used to weld most metals such as steel, aluminum, copper and nickel alloys, titanium, and cobalt. It is the most commonly used type of welding because it can weld materials cleanly and maintains a high level of purity that isn’t achievable through other methods of welding.
One of the advantages of this type of welding is that it can weld materials that are very thin and offer a clean weld of high quality. They can also be used across a wide range of alloys.
Flux Cored Arc Welding (FCAW)
This type of arc welding has similarities with the Metal Inert Gas (MIG) welding method. It constantly requires an electrode to be fed but instead of using a solid wire, it uses a tube-shaped wire that is full of flux. The two types of flux core wires are socially and double shield wires.
For outdoor use, social good wires are recommended because they can be used even if it is windy. This type of welding gives the user a higher electrode efficiency because it generates less waste. An external shield gas is unnecessary and therefore, fewer welding fumes are generated.
However, a lot of smoke can be generated by this type of welding method and the equipment is expensive.
Shielded Metal Arc Welding (SMAW)
This is a welding technique that carries electric current through an electrode so that most of the weld metal is provided. A coded influx core wire and electric arc is created as soon as the electrode’s tip is placed on the work piece and removed, but it still creates temperatures as high as 6500°F.
SMAW’s main advantage is its portability as well as the low cost of needed equipment. Shielding gas is unnecessary so it can be used outdoors even when there is wind and rain. It can also be used on metals that are rusty or dirty, unlike the MIG and TIG techniques.
However, a lot of waste is produced in this welding technique and the user or operator has to be highly skilled in order to pull it off. And unlike the neat welding that comes from the TIG technique, materials that undergo SMAW may not look their best once the project is finished. It can lead to porosity, shallow penetration, cracking, and it cannot withstand severe weather.
Plasma Arc Welding
Plasma arc welding is similar to TIG welding, but instead, it involves the recession of an electrode and the ionizing gases inside the arc in order to create heat. Electrical current passes through a small nozzle for extreme accuracy. Usually used by the aircraft manufacturing industry, t is recommended for welding small areas and is rarely used by DIY welders.
Other methods of arc welding include:
- Submerged Arc Welding (SAW)
- Gas Tungsten Arc Welding (GTAW)
- Metal Active Gas (MAG) Welding
- Gas Metal Arc Welding (GMAW)
Friction Welding
Friction welding combines or joins materials together through the use of mechanical friction. It can be used on materials such as aluminum, steel—and surprisingly, wood. Heat is generated in order to soften the materials. As they cool, a bond is created.
No filler metals or gas for shielding or flux is needed in friction welding. It has great applications for light-weight aluminum alloys which would otherwise be considered “non-weldable.”
Electron Beam Welding
Electron beam welding uses a high velocity beam of electrons in order to join materials. The electrons’ kinetic energy changes into heat, allowing the materials to melt into one another.
This kind of welding is usually done in a vacuum through the use of a vacuum chamber so that the beam does not dissipate. It is recommended for the joining of sections that are too thick and is commonly used in the aerospace and nuclear power industry.
It can also be applied to the automotive and rail industries.
Laser Beam Welding
A laser provides concentrated heat that gives way for deep welds, barrow, and high joining rates. Laser beam welding is easily automated, making it a great option for industries that produce materials in high volumes.
Unlike electron beam welding, which is done in a vacuum, laser beam welding is done in the air and is commonly used to join pieces of metal or thermoplastics.
Resistance Welding
This is another process that can quickly weld materials. There are two types:
Resistance Spot Welding
Heat is delivered between two electrodes, which in turn is placed on a small area while the materials are clamped together.
Resistance Seam Welding
It is similar to resistance spot welding, but the electrodes are replaced with rotating wheels to that the weld remains leak-free.
What is the strongest kind of weld?
When determining the strongest type of weld, it actually depends on the base material being used for the welding. Each welding technique comes with its own sets of pros and cons.
If we were to choose which weld yields the strongest, stick welding might just be the best. This only counts the pure strength and the material’s thickness because stick welding is the only type that can weld cast iron. Plus, it can be used on materials that are dirty, and can be used outdoors even with bad weather conditions.
However, stick welding can’t always be the best welding option.
MIG welding can be used on a large selection of metals that have varying thicknesses and TIG welding is a technique that produces a high welding quality, particularly with thin metals. Between MIG and TIG welding, TIG produces the best results.
Stainless steel welding lays down another set of circumstances because stainless steel is beefier if you compare it to aluminum. When talking about welding thicker sheets of stainless steel, we have to consider another welding technique. In this case, stick and flux welding is the best choice.
Otherwise, if the steel isn’t as thick and is comparatively milder, TIG and MIG welding techniques may be applied.
Which method of welding is the easiest to learn?
MIG welding seems to be the easiest type of welding to learn because its welds are clean and have a power output with a high adjustability. It also doesn’t take that much time when you’re using it. Those who are still practicing their welding speak about how simple and reliable MIG welding is when you are just a beginner,
Just because MIG welding is the easiest to learn, doesn’t mean you should close yourself off to other welding techniques. There is a machine called a hybrid welder that allows you to experiment different kinds of techniques all from one tool.
Conclusion
The different kinds of welding can be specifically catered to an industry. Subsequently, these welding types can have different process across different industries. Each one comes with its own list of pros and cons, so be sure to familiarize yourself with what you can do, and what you can afford.
Get the right training before trying to weld anything, and always wear your personal protective equipment to avoid long-term health conditions as well as severe burns and other injuries.
Educate yourself with the techniques used in your industry and always place your safety above everything else.